Movable stacking type automatic stereoscopic warehouse
A stacking and automatic technology, applied in the field of three-dimensional warehouse, can solve the problems of slow loading and unloading of goods, complex fork structure, long time consumption, etc., to improve the speed of loading and unloading, simple structure and low manufacturing cost. Effect
- Summary
- Abstract
- Description
- Claims
- Application Information
AI Technical Summary
Problems solved by technology
Method used
Image
Examples
Embodiment Construction
[0019] The present invention will be further described below in conjunction with the accompanying drawings and examples, but the examples do not constitute a limitation to the present invention.
[0020] Figure 1 to Figure 4 It shows the first embodiment of a mobile stacking type automatic vertical warehouse of the present invention, which includes three columns and three layers of penetrating storage shelves 1, a shuttle car 2 that travels on the guide rail of the shelf 1, and can move at the end of the shelf 1 to face each A roadway stacker 3 and a roller conveyor 4 for the operation of the racks. The roadway stacker 3 includes a traveling trolley 18, a frame 5 vertically installed on the traveling trolley 18 and a lifting platform 6 that lifts along the frame 5 , a shuttle car guide rail 7 is installed on the left side of the lifting platform 6, and a shuttle car guide rail 8 is installed on the right side. The upper part of the shuttle car guide rail is provided with a sh...
PUM
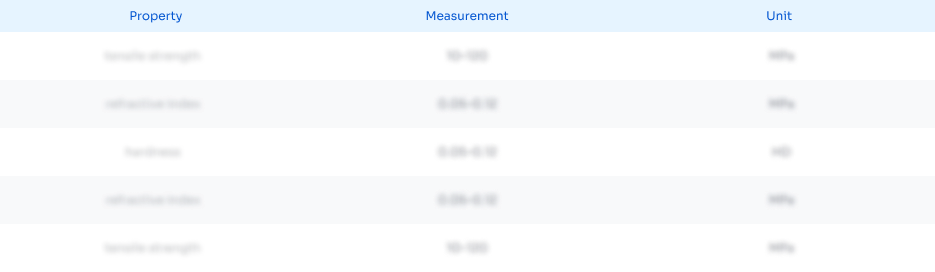
Abstract
Description
Claims
Application Information

- R&D Engineer
- R&D Manager
- IP Professional
- Industry Leading Data Capabilities
- Powerful AI technology
- Patent DNA Extraction
Browse by: Latest US Patents, China's latest patents, Technical Efficacy Thesaurus, Application Domain, Technology Topic, Popular Technical Reports.
© 2024 PatSnap. All rights reserved.Legal|Privacy policy|Modern Slavery Act Transparency Statement|Sitemap|About US| Contact US: help@patsnap.com