Heat conduction transparent modification process of epoxy resin for LED packaging
An epoxy resin and modification technology, which is applied in the field of thermal conductivity and transparent modification process of epoxy resin for LED packaging, can solve the problems such as the inability of graphite to be used.
- Summary
- Abstract
- Description
- Claims
- Application Information
AI Technical Summary
Problems solved by technology
Method used
Examples
Embodiment Construction
[0012] In order to make the object, technical solution and advantages of the present invention more clear, the present invention will be further described in detail below in conjunction with the examples. It should be understood that the specific embodiments described here are only used to explain the present invention, not to limit the invention.
[0013] Thermally conductive and transparent modification process of epoxy resin for LED packaging. The process adopts the precipitation transformation method, using brine and sodium carbonate as raw materials, and polyvinyl alcohol (PVA) as a modifier to prepare nano-magnesia particles with good dispersion. Using nano-MgO (magnesium oxide) as filler, adding epoxy resin to the AB glue curing system to enhance the thermal conductivity of the cured product, the steps of preparing nano-magnesia particles and modifying and curing epoxy resin are:
[0014] (1) Preparation of nano magnesium oxide particles;
[0015] Prepare...
PUM
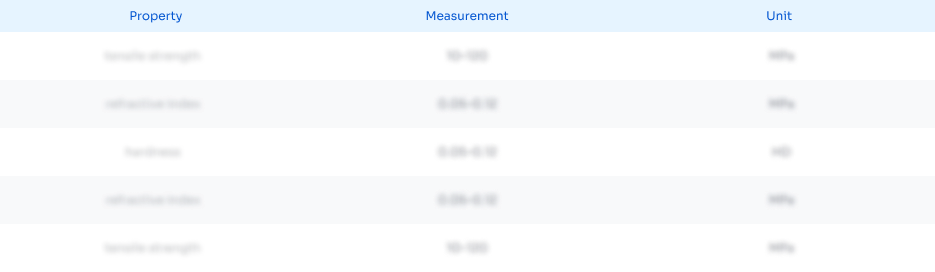
Abstract
Description
Claims
Application Information

- R&D
- Intellectual Property
- Life Sciences
- Materials
- Tech Scout
- Unparalleled Data Quality
- Higher Quality Content
- 60% Fewer Hallucinations
Browse by: Latest US Patents, China's latest patents, Technical Efficacy Thesaurus, Application Domain, Technology Topic, Popular Technical Reports.
© 2025 PatSnap. All rights reserved.Legal|Privacy policy|Modern Slavery Act Transparency Statement|Sitemap|About US| Contact US: help@patsnap.com