Sludge dewatering flocculant and its dewatering method
A sludge dehydration and flocculant technology, applied in the direction of dehydration/drying/concentrated sludge treatment, etc., can solve the problems of unsatisfactory effect, achieve the effect of improving dehydration effect, reducing toxic and harmful substances, and enhancing flocculation performance
- Summary
- Abstract
- Description
- Claims
- Application Information
AI Technical Summary
Problems solved by technology
Method used
Image
Examples
Embodiment 1
[0017] The sludge dewatering flocculant is composed of agent A and agent B; the agent A is made of the following raw materials in parts by weight: 28 parts of ferrous sulfate, 10 parts of heavy metal scavenger, 43 parts of blue carbon, 12 parts of lime powder, 12 parts of alkylamine polyoxyethylene ether phosphate, 9 parts of lignosulfonate;
[0018] The agent B is prepared from the following raw materials in parts by weight: 35 parts of betaine, 20 parts of tetraethylenepentamine, 9 parts of formaldehyde, 9 parts of ethanol and 55 parts of water.
[0019] The preparation method of the A agent comprises: grinding ferrous sulfate, semi-coke, and lime powder through a 500-mesh sieve, and then mixing and stirring evenly with the heavy metal scavenger, alkylamine polyoxyethylene ether phosphate, and lignosulfonate.
[0020] The preparation method of the B agent includes adding tetraethylenepentamine and ethanol into the reaction kettle and stirring until the tetraethylenepentamine...
Embodiment 2
[0026] The sludge dewatering flocculant is composed of agent A and agent B; the agent A is made of the following raw materials in parts by weight: 20 parts of ferrous sulfate, 6 parts of heavy metal scavenger, 42 parts of blue carbon, 15 parts of lime powder, 14 parts of alkylamine polyoxyethylene ether phosphate, 6 parts of lignosulfonate;
[0027] The B agent is made of the following raw materials in parts by weight: 37 parts of betaine, 15 parts of tetraethylenepentamine, 8 parts of formaldehyde, 15 parts of ethanol, and 45 parts of water.
[0028] The preparation method of the A agent comprises: grinding ferrous sulfate, semi-coke, and lime powder through a 500-mesh sieve, and then mixing and stirring evenly with the heavy metal scavenger, alkylamine polyoxyethylene ether phosphate, and lignosulfonate.
[0029] The preparation method of the B agent includes adding tetraethylenepentamine and ethanol into the reaction kettle and stirring until the tetraethylenepentamine is d...
Embodiment 3
[0035] The sludge dewatering flocculant is composed of agent A and agent B; the agent A is made of the following raw materials in parts by weight: 25 parts of ferrous sulfate, 8 parts of heavy metal scavenger, 45 parts of blue carbon, 17 parts of lime powder, 10 parts of alkylamine polyoxyethylene ether phosphate, 4 parts of lignosulfonate;
[0036] The B agent is made of the following raw materials in parts by weight: 40 parts of betaine, 23 parts of tetraethylenepentamine, 10 parts of formaldehyde, 10 parts of ethanol, and 50 parts of water.
[0037] The preparation method of the A agent comprises: grinding ferrous sulfate, semi-coke, and lime powder through a 500-mesh sieve, and then mixing and stirring evenly with the heavy metal scavenger, alkylamine polyoxyethylene ether phosphate, and lignosulfonate.
[0038] The preparation method of the B agent includes adding tetraethylenepentamine and ethanol into the reaction kettle and stirring until the tetraethylenepentamine is ...
PUM
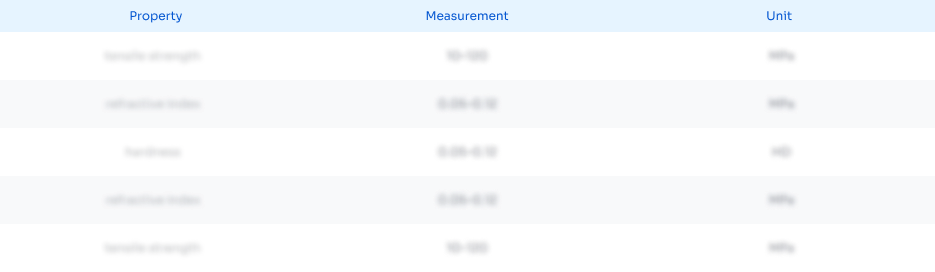
Abstract
Description
Claims
Application Information

- R&D
- Intellectual Property
- Life Sciences
- Materials
- Tech Scout
- Unparalleled Data Quality
- Higher Quality Content
- 60% Fewer Hallucinations
Browse by: Latest US Patents, China's latest patents, Technical Efficacy Thesaurus, Application Domain, Technology Topic, Popular Technical Reports.
© 2025 PatSnap. All rights reserved.Legal|Privacy policy|Modern Slavery Act Transparency Statement|Sitemap|About US| Contact US: help@patsnap.com