Treatment method of high-salt content, high-ammonia nitrogen content and high-COD (Chemical Oxygen Demand) gas field water
A treatment method and technology for gas field water, which can be applied in mining wastewater treatment, water/sewage multi-stage treatment, water/sludge/sewage treatment, etc., which can solve the problem that membranes are easily polluted, the cost of treatment and operation increases, and the difficulty of ion exchange resins. And other issues
- Summary
- Abstract
- Description
- Claims
- Application Information
AI Technical Summary
Problems solved by technology
Method used
Image
Examples
Embodiment 1
[0040] refer to figure 1 As shown, the gas field water whose main components are shown in Table 4 is used as raw material, and NaOH and NaOH are added 2 CO 3Remove calcium and magnesium, adjust the pH to 11.53, pump 350L of calcium and magnesium clear liquid into the 500L evaporator, control the temperature of the evaporation material liquid at 101°C, stop evaporation when the condensed water reaches 35L, and drain the condensed water for a period of time. Vacuum evaporation and concentration, control the boiling point above 45°C, collect the condensed water in the second stage, when the volume of the concentrated feed liquid is concentrated to 100L, transfer 90L of the concentrated feed liquid to a 100L evaporator and continue to concentrate until the salt crystallizes, and the remaining 10L of the concentrated feed liquid is set aside. After the discharged salt slurry is washed and flotation with the remaining 10L of concentrated feed liquid, the mother liquor enters the el...
Embodiment 2
[0048] Using gas field water whose main components are shown in Table 7 as raw material, add NaOH and NaOH 2 CO 3 Remove calcium and magnesium, adjust the pH to 11.21, pump 350L of calcium and magnesium clear liquid into the 500L evaporator, control the temperature of the evaporation material liquid at 95°C, stop evaporation when the condensed water reaches 52L, and drain the condensed water for a period of time. Vacuum evaporation and concentration, control the boiling point to be above 45°C, collect the condensed water in the second stage, when the volume of the concentrated feed liquid is concentrated to 100L, transfer 90L of the concentrated feed liquid to a 100L evaporator and continue to concentrate until the salt crystallizes, and the remaining 10L of the concentrated feed liquid is for use . After the discharged salt slurry is washed and flotation with the remaining 10L of concentrated feed liquid, the mother liquor enters the electrolytic catalytic oxidation device t...
Embodiment 3
[0056] Using gas field water whose main components are shown in Table 10 as raw material, add NaOH and NaOH 2 CO 3 Remove calcium and magnesium, adjust the pH to 11.04, pump 350L of calcium and magnesium clear liquid into the 500L evaporator, control the temperature of the evaporation material liquid at 90°C, stop evaporation when the condensed water reaches 70L, and drain the condensed water for a period of time. Vacuum evaporation and concentration, control the boiling point to be above 45°C, collect the condensed water in the second stage, when the volume of the concentrated feed liquid is concentrated to 100L, transfer 90L of the concentrated feed liquid to a 100L evaporator and continue to concentrate until the salt crystallizes, and the remaining 10L of the concentrated feed liquid is for use . After the discharged salt slurry is washed and flotation with the remaining 10L of concentrated feed liquid, the mother liquor enters the electrolytic catalytic oxidation device ...
PUM
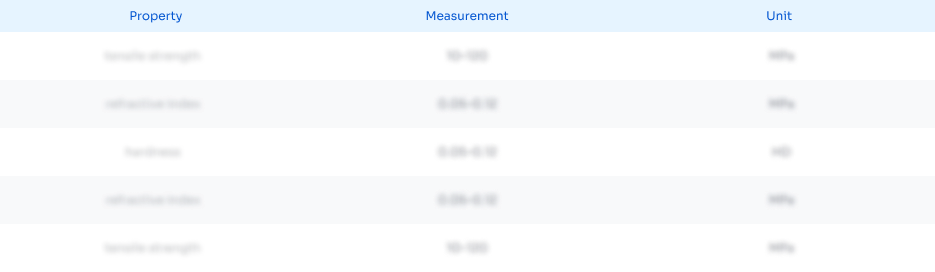
Abstract
Description
Claims
Application Information

- Generate Ideas
- Intellectual Property
- Life Sciences
- Materials
- Tech Scout
- Unparalleled Data Quality
- Higher Quality Content
- 60% Fewer Hallucinations
Browse by: Latest US Patents, China's latest patents, Technical Efficacy Thesaurus, Application Domain, Technology Topic, Popular Technical Reports.
© 2025 PatSnap. All rights reserved.Legal|Privacy policy|Modern Slavery Act Transparency Statement|Sitemap|About US| Contact US: help@patsnap.com