Three rotating decoupling spherical surface parallel robot mechanism
A robot and three-rotation technology, applied in the field of robots, can solve the problems of limiting the application of parallel mechanisms, designing the configuration of parallel mechanisms, analyzing and calculating the control difficulties of the mechanism, and achieving the effects of simple structure, high strength and good stability
- Summary
- Abstract
- Description
- Claims
- Application Information
AI Technical Summary
Problems solved by technology
Method used
Image
Examples
Embodiment Construction
[0011] exist figure 1 In the schematic diagram of the three-rotation decoupling spherical parallel robot mechanism shown, one end of the arc-shaped connecting rod at one end of each branch passes through the first rotating pair R 1 Connected with the base 8, the other end of the arc-shaped connecting rod 1 of the branch 1 passes through the second rotating pair R 12 It is connected with one end of right-angled connecting rod one 2, and the other end of the right-angled connecting rod one passes through the third rotating pair R 13 It is connected with one end of the right-angled connecting rod 2 3, and the other end of the right-angled connecting rod 2 passes through the fourth rotating pair R 14 Connected with the moving platform 9, the axes of the two adjacent rotating pairs in the above-mentioned one-half are perpendicular to each other; the other end of the arc-shaped connecting rod 4 of the second branch passes through the second rotating pair R 22 It is connected with ...
PUM
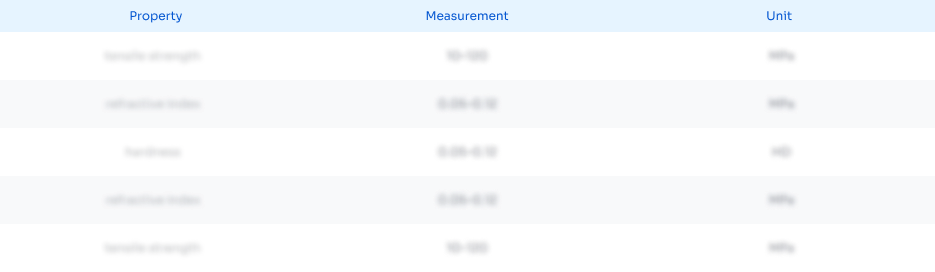
Abstract
Description
Claims
Application Information

- Generate Ideas
- Intellectual Property
- Life Sciences
- Materials
- Tech Scout
- Unparalleled Data Quality
- Higher Quality Content
- 60% Fewer Hallucinations
Browse by: Latest US Patents, China's latest patents, Technical Efficacy Thesaurus, Application Domain, Technology Topic, Popular Technical Reports.
© 2025 PatSnap. All rights reserved.Legal|Privacy policy|Modern Slavery Act Transparency Statement|Sitemap|About US| Contact US: help@patsnap.com