Magneto-rheological damping structure for rotating motion transmission components
A technology for damping structures and transmission components, applied in the direction of rotation vibration suppression, shock absorbers, shock absorbers, etc., can solve the problems of reducing the service life of devices, generating noise, and wear of parts, so as to achieve strong adaptability and reduce noise , the effect of simple structure
- Summary
- Abstract
- Description
- Claims
- Application Information
AI Technical Summary
Problems solved by technology
Method used
Image
Examples
Embodiment Construction
[0018] figure 1 It is a schematic diagram of the magnetorheological vibration damping structure for rotating transmission components of the present invention, figure 2 It is the magnetorheological vibration damping structure of the present invention for rotating motion transmission components. figure 1 A schematic diagram of A-A direction, image 3 It is a three-dimensional cross-sectional view of a mounting structure for the excitation source of the magnetorheological vibration damping structure of the rotational motion transmission component of the present invention, Figure 4 It is a three-dimensional cross-sectional view of another installation structure of the excitation source of the magnetorheological vibration reduction structure for the rotary motion transmission part of the present invention, as shown in the figure: the magnetorheological reduction for the rotary motion transmission part of this embodiment The vibration structure includes an inner core 1 and an outer sh...
PUM
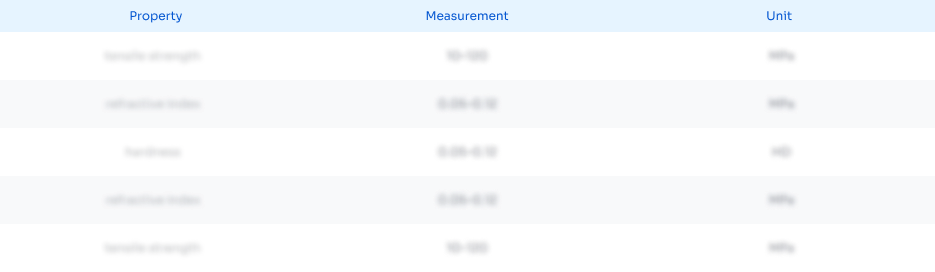
Abstract
Description
Claims
Application Information

- R&D Engineer
- R&D Manager
- IP Professional
- Industry Leading Data Capabilities
- Powerful AI technology
- Patent DNA Extraction
Browse by: Latest US Patents, China's latest patents, Technical Efficacy Thesaurus, Application Domain, Technology Topic, Popular Technical Reports.
© 2024 PatSnap. All rights reserved.Legal|Privacy policy|Modern Slavery Act Transparency Statement|Sitemap|About US| Contact US: help@patsnap.com