Method for controlling position of pinch roll at finish rolling inlet of hot continuous rolling device
A technology of hot continuous rolling mill and control method, which is applied in the direction of rolling mill control device, rolling force/roll gap control, metal rolling, etc., which can solve the problems of low efficiency and poor control accuracy of manual control methods, and achieve fast and accurate control , to achieve the effect of precision control
- Summary
- Abstract
- Description
- Claims
- Application Information
AI Technical Summary
Problems solved by technology
Method used
Image
Examples
Embodiment Construction
[0042] The present invention will be described in further detail below in conjunction with the accompanying drawings.
[0043] The structure of the pinch roller is as figure 2 As shown, including the upper roll and the lower roll, the upper roll is fixed, in contact with the strip steel, always rotates during rolling, and the speed is consistent with the speed of the strip steel, the lower roll is movable up and down, and the pinch roll Two hydraulic cylinders are respectively installed on the operation side and the transmission side. The pinch roller is driven by the hydraulic cylinders on the transmission side and the operation side to complete the positioning of the roll gap. Each hydraulic cylinder is equipped with a position sensor for measuring the position of the hydraulic cylinder. actual location.
[0044]In the actual production process, since the control of the pinch roller gap is completed by the hydraulic cylinder, when the oil cylinder leaks, the sensor zero dr...
PUM
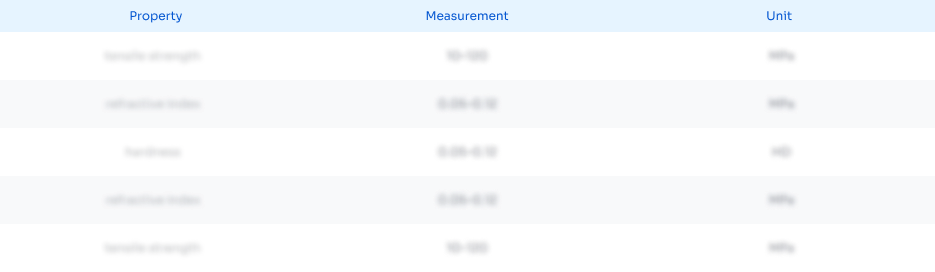
Abstract
Description
Claims
Application Information

- R&D
- Intellectual Property
- Life Sciences
- Materials
- Tech Scout
- Unparalleled Data Quality
- Higher Quality Content
- 60% Fewer Hallucinations
Browse by: Latest US Patents, China's latest patents, Technical Efficacy Thesaurus, Application Domain, Technology Topic, Popular Technical Reports.
© 2025 PatSnap. All rights reserved.Legal|Privacy policy|Modern Slavery Act Transparency Statement|Sitemap|About US| Contact US: help@patsnap.com