Rigidity-adjustable semi-active control type torsional damper for vehicle
A semi-active control, torsional damper technology, applied in the direction of shock absorber, spring/shock absorber, vibration suppression adjustment, etc., can solve the problem of low stiffness, limited vibration frequency band of passive torsional damper, and difficult vibration damping effect There are problems such as further improvement to achieve the effect of solving contradictions and benefiting safety and comfort
- Summary
- Abstract
- Description
- Claims
- Application Information
AI Technical Summary
Problems solved by technology
Method used
Image
Examples
Embodiment
[0033] Such as Figure 6 As shown: the force transmitted to the force transmission cylinder 10 is provided by two magnets, wherein the magnet located below is fixed on the slider 9 and can move up and down with the movement of the force transmission cylinder 10. When the force transmission cylinder 10 moves up and down, the two The distance of the magnet changes accordingly, and the magnitude of the force also changes; at the same time, this part of the magnet can also be replaced with an electromagnet, and the interaction force between the electromagnets is controlled by the controller 13 to control the current, and the negative stiffness structure is adjusted The size of the force makes the stiffness of the mechanism with positive and negative stiffness in parallel be in a state of quasi-zero stiffness, realizing broadband vibration reduction.
[0034] work process:
[0035] When the shock absorber is not working, the dome gear teeth 11 at the negative stiffness structure pos...
PUM
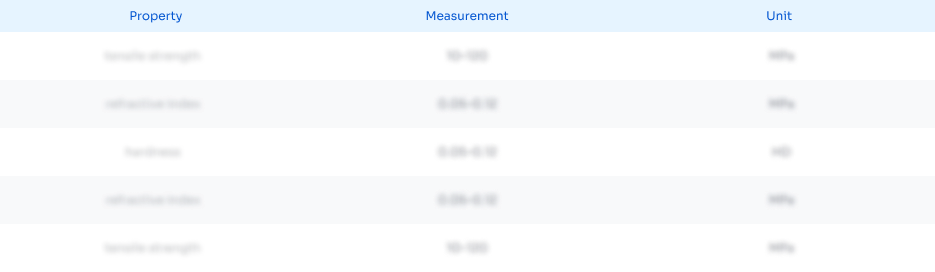
Abstract
Description
Claims
Application Information

- R&D
- Intellectual Property
- Life Sciences
- Materials
- Tech Scout
- Unparalleled Data Quality
- Higher Quality Content
- 60% Fewer Hallucinations
Browse by: Latest US Patents, China's latest patents, Technical Efficacy Thesaurus, Application Domain, Technology Topic, Popular Technical Reports.
© 2025 PatSnap. All rights reserved.Legal|Privacy policy|Modern Slavery Act Transparency Statement|Sitemap|About US| Contact US: help@patsnap.com