Method for analyzing service life of high maneuverability aircraft base on detail fatigue rating
A life analysis and rating technology, applied in the field of aircraft fatigue, can solve the problems of life analysis and different reliability indicators that cannot be directly applied to high-mobility aircraft, and achieve the effects of shortening the development cycle, less calculation workload, and significant economic benefits
- Summary
- Abstract
- Description
- Claims
- Application Information
AI Technical Summary
Problems solved by technology
Method used
Image
Examples
Embodiment Construction
[0053] The present invention will be described in further detail below through specific embodiments and in conjunction with the accompanying drawings.
[0054] The following is an example of the life calculation of the outer wing lower panel of a high maneuvering aircraft.
[0055] First, compile the load spectrum for detailed fatigue rating analysis based on the random spectrum of this type of aircraft
[0056] A basic spectrum block of the random spectrum of this type of aircraft consists of 12 typical subjects, a total of 131 takeoffs and landings, representing 176.333 flight hours. In order to ensure the integrity of the basic spectrum blocks, a spectrum with 12167 flight hours as a complete cycle was constructed, including 69 basic spectrum blocks, and the number of load cycles was 228495 times.
[0057] The complete load cycle is extracted by the rainflow counting method, and m=4 is taken. According to the selection principle and method of the standard constant amplitud...
PUM
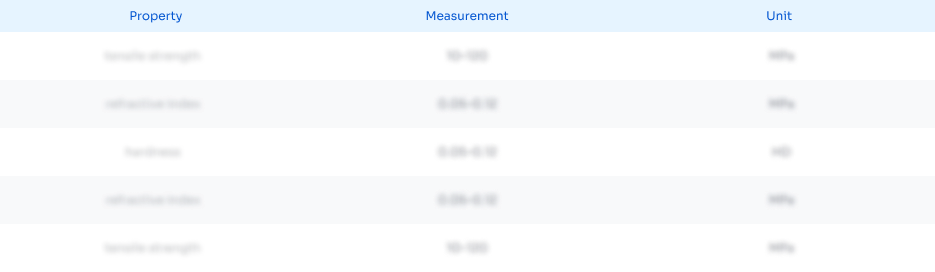
Abstract
Description
Claims
Application Information

- R&D
- Intellectual Property
- Life Sciences
- Materials
- Tech Scout
- Unparalleled Data Quality
- Higher Quality Content
- 60% Fewer Hallucinations
Browse by: Latest US Patents, China's latest patents, Technical Efficacy Thesaurus, Application Domain, Technology Topic, Popular Technical Reports.
© 2025 PatSnap. All rights reserved.Legal|Privacy policy|Modern Slavery Act Transparency Statement|Sitemap|About US| Contact US: help@patsnap.com