A kind of reel type optical unit optical cable and its manufacturing process
A manufacturing process and optical unit technology, applied in the direction of optical components, optics, light guides, etc., can solve the problems of difficulty in laying, time-consuming and labor-intensive installation and laying, and cost of construction time, etc., to achieve convenient and fast construction connection, easy construction and laying, and low bending radius small effect
- Summary
- Abstract
- Description
- Claims
- Application Information
AI Technical Summary
Problems solved by technology
Method used
Image
Examples
Embodiment Construction
[0021] Such as Figure 1-8 As shown, a reel-type optical unit optical cable, the optical unit optical cable includes an optical unit 6 and a jacket layer 5, the optical unit includes a reel-type optical fiber ribbon 2, and the center of the reel-type optical fiber ribbon is a Aramid fiber 1, the roll-type optical fiber ribbon is wrapped with water-blocking material, cable tie 3, and sleeve 4 in sequence.
[0022] A manufacturing process of a tape-and-reel optical unit optical cable, comprising the following steps: 1. Making a number of 200µm optical fibers into a mesh-shaped and bonded optical fiber ribbon 7 through a specific ribbon mould; 2. The optical fiber ribbon is slowly rolled into a closed circle through a U-shaped horn mold 12 with a smooth surface made of ceramics, and the optical fiber column 8 is formed through a shaping mold 13 made of ceramics. Put the material into the casing to form an optical unit after being tied up; 3. Make a tape-type central tube optical...
PUM
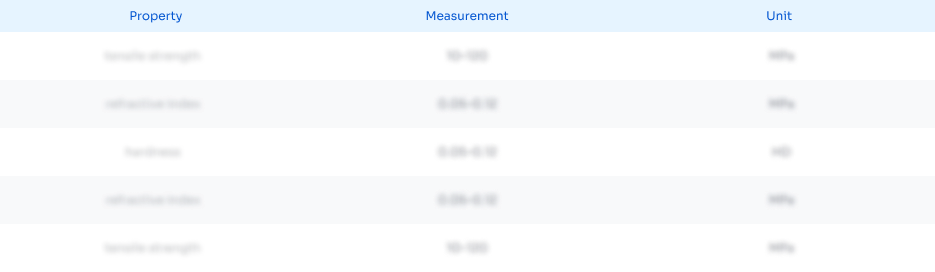
Abstract
Description
Claims
Application Information

- Generate Ideas
- Intellectual Property
- Life Sciences
- Materials
- Tech Scout
- Unparalleled Data Quality
- Higher Quality Content
- 60% Fewer Hallucinations
Browse by: Latest US Patents, China's latest patents, Technical Efficacy Thesaurus, Application Domain, Technology Topic, Popular Technical Reports.
© 2025 PatSnap. All rights reserved.Legal|Privacy policy|Modern Slavery Act Transparency Statement|Sitemap|About US| Contact US: help@patsnap.com