Roller kiln and working method thereof
A technology of roller kiln and kiln roof, applied in combustion method, furnace type, waste heat treatment, etc., can solve the problems of low utilization rate of waste heat of roller kiln, poor production environment, high cost, and reduce investment cost and maintenance and repair cost. , The effect of short conveying distance and reducing operating costs
- Summary
- Abstract
- Description
- Claims
- Application Information
AI Technical Summary
Problems solved by technology
Method used
Image
Examples
Embodiment Construction
[0041] The following will clearly and completely describe the technical solutions in the embodiments of the present invention. Obviously, the described embodiments are only some of the embodiments of the present invention, rather than all the embodiments. Based on the embodiments of the present invention, all other embodiments obtained by persons of ordinary skill in the art without making creative efforts belong to the protection scope of the present invention.
[0042] see figure 1 , is a schematic diagram of the three-dimensional structure of the roller kiln provided by the present invention. The roller kiln 1 includes a kiln bottom 100, a side wall 200, a kiln roof 300, and a transmission roller device 400, and two opposite side walls 200 are sandwiched between the kiln roof 300 and the kiln bottom 100 It also encloses a kiln storage space 500 with openings at both ends. The transmission roller device 400 is connected to two oppositely arranged side walls 200. The transmi...
PUM
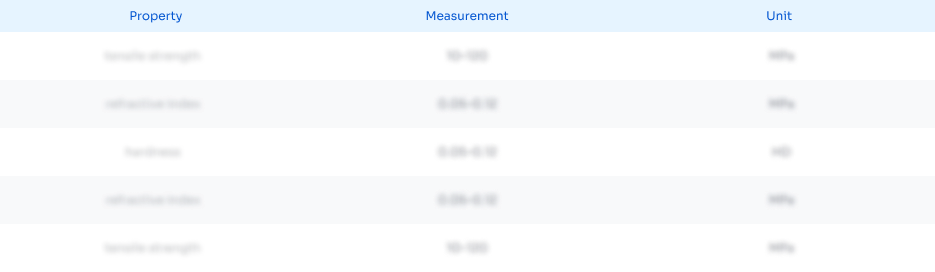
Abstract
Description
Claims
Application Information

- Generate Ideas
- Intellectual Property
- Life Sciences
- Materials
- Tech Scout
- Unparalleled Data Quality
- Higher Quality Content
- 60% Fewer Hallucinations
Browse by: Latest US Patents, China's latest patents, Technical Efficacy Thesaurus, Application Domain, Technology Topic, Popular Technical Reports.
© 2025 PatSnap. All rights reserved.Legal|Privacy policy|Modern Slavery Act Transparency Statement|Sitemap|About US| Contact US: help@patsnap.com