Method for operating a drive unit for a hybrid vehicle
A technology of hybrid electric vehicles and drive units, which is applied to the layout of multiple different prime movers of hybrid electric vehicles and general power plants, and motor vehicles, and can solve the problems of joint impact and discomfort, so as to avoid joint impact and avoid discomfort. Comfortable joining impact, comfort improvement effect
- Summary
- Abstract
- Description
- Claims
- Application Information
AI Technical Summary
Problems solved by technology
Method used
Image
Examples
Embodiment Construction
[0030] figure 1 A schematic diagram showing a drive unit for a hybrid vehicle. figure 1 The drive unit comprises a drive unit 3 formed by an internal combustion engine 1 and an electric machine 2 , wherein a transmission 5 is connected between the drive unit 3 and an output 4 . The transmission 5 comprises two sub-transmissions 6 and 7, which are so to speak parallel to each other, wherein, in the embodiment shown, the first sub-transmission 6 provides the forward gears "1", "3", "5" and "7", while the second sub-transmission 7 provides forward gears "2", "4", "6" and reverse gear "R". sub-transmissions 6 and 7 in the figure 1 The gear sets shown in and the shown assignment of the gears to the two subtransmissions are exemplary properties.
[0031] To provide forward and reverse gears, the subtransmissions 6 and 7 of the transmission 5 include form-fitting shifting elements 13 , also called shifting elements. The construction and arrangement of the subtransmissions 6 and 7...
PUM
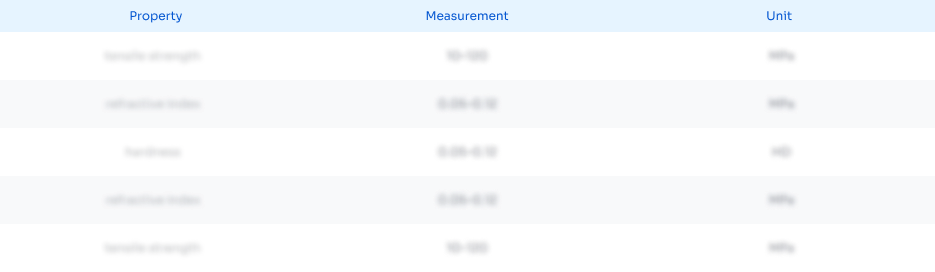
Abstract
Description
Claims
Application Information

- Generate Ideas
- Intellectual Property
- Life Sciences
- Materials
- Tech Scout
- Unparalleled Data Quality
- Higher Quality Content
- 60% Fewer Hallucinations
Browse by: Latest US Patents, China's latest patents, Technical Efficacy Thesaurus, Application Domain, Technology Topic, Popular Technical Reports.
© 2025 PatSnap. All rights reserved.Legal|Privacy policy|Modern Slavery Act Transparency Statement|Sitemap|About US| Contact US: help@patsnap.com