Internal supercharging method for composite material multi-rib siding structure cementing forming technology
A composite material and molding process technology, applied in the field of composite material manufacturing
- Summary
- Abstract
- Description
- Claims
- Application Information
AI Technical Summary
Problems solved by technology
Method used
Image
Examples
Embodiment Construction
[0009] The present invention will be described in further detail below in conjunction with the accompanying drawings and specific embodiments.
[0010] as attached figure 1 , 2 As shown, a composite material multi-rib panel structure adhesive bonding molding process internal pressurization method, the composite material multi-rib panel structure includes an upper skin panel 1, a wall body 2, a lower skin panel panel 3, and a wall body 2 The upper and lower skin panels 1 and 3 adopt the double-sided rubber mold 4 secondary bonding molding process, but because the flange of the wall 2 shrinks downward (upward), there is a gap with the upper and lower skin panels 1 and 3, which cannot To ensure the quality of the bonding, in the inner cavity of the wall 2, the internal pressurization method of combining the metal mandrel 5, the silicone rubber plate 6 and the expansion rubber plate 7 is used, and the silicone rubber plate 6 and the expansion rubber plate 7 are used as ...
PUM
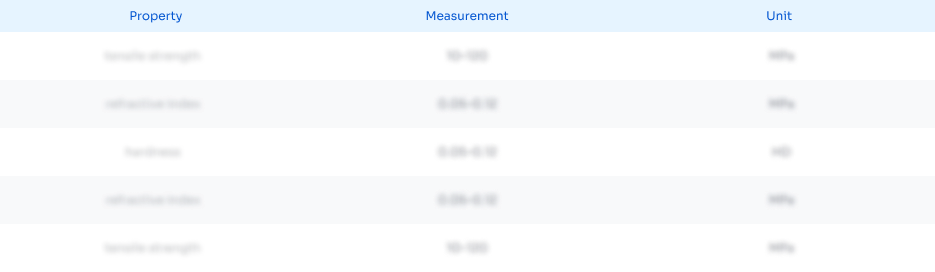
Abstract
Description
Claims
Application Information

- R&D
- Intellectual Property
- Life Sciences
- Materials
- Tech Scout
- Unparalleled Data Quality
- Higher Quality Content
- 60% Fewer Hallucinations
Browse by: Latest US Patents, China's latest patents, Technical Efficacy Thesaurus, Application Domain, Technology Topic, Popular Technical Reports.
© 2025 PatSnap. All rights reserved.Legal|Privacy policy|Modern Slavery Act Transparency Statement|Sitemap|About US| Contact US: help@patsnap.com