Full-automatic bidirectional stacker robot
A palletizing robot, fully automatic technology, applied in the direction of manipulator, object stacking, object destacking, etc., can solve the problems of high manufacturing and processing costs, heavy balance device, complex mechanical arm structure, etc., to avoid accidental damage , Reduce production costs, and the packaging effect is firm
- Summary
- Abstract
- Description
- Claims
- Application Information
AI Technical Summary
Problems solved by technology
Method used
Image
Examples
Embodiment Construction
[0018] Below in conjunction with accompanying drawing, the present invention is described in further detail:
[0019] Such as figure 1 , 2 As shown, a fully automatic two-way palletizing robot of the present invention includes a base 1 on which a toothed disc 2 is rotatably connected, and the base 1 on one side of the toothed disc 2 is provided with a A propulsion screw 3 that can drive the toothed plate 2 to rotate. The toothed plate 2 is vertically provided with a lifting screw 5 and a column 4 with a lifting slide rail. The thread of the lifting screw 5 is matched with a telescopic cross arm 6 that can slide along the lifting slide rail. , one end of the telescopic cross arm 6 is provided with a counterweight, the telescopic cross arm 6 is provided with a translation slide rail and a translation screw 7 in parallel, and the translation screw 7 is threaded with a slider 10 that can slide along the translation slide rail, the slider 10 The front end is connected with a supp...
PUM
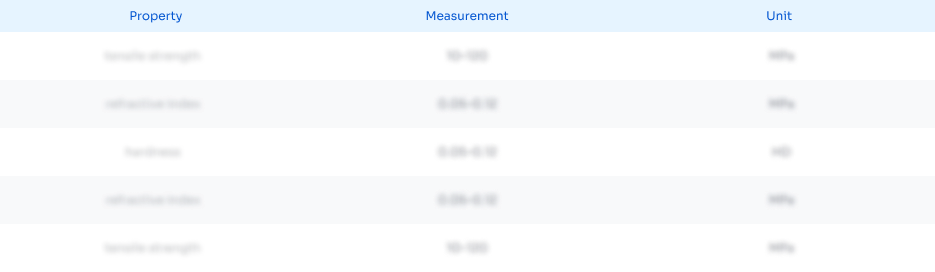
Abstract
Description
Claims
Application Information

- R&D Engineer
- R&D Manager
- IP Professional
- Industry Leading Data Capabilities
- Powerful AI technology
- Patent DNA Extraction
Browse by: Latest US Patents, China's latest patents, Technical Efficacy Thesaurus, Application Domain, Technology Topic, Popular Technical Reports.
© 2024 PatSnap. All rights reserved.Legal|Privacy policy|Modern Slavery Act Transparency Statement|Sitemap|About US| Contact US: help@patsnap.com