Metal alternate extrusion forming device and method
An extrusion forming and metal technology, which is applied in the field of labor-saving extrusion forming devices, can solve the problems of low material utilization rate, high energy consumption, poor flow uniformity, etc., and achieve the improvement of material utilization rate, flow uniformity, and extrusion load Reduced effect
- Summary
- Abstract
- Description
- Claims
- Application Information
AI Technical Summary
Problems solved by technology
Method used
Image
Examples
specific Embodiment approach 1
[0021] Specific implementation mode one: combine figure 1 Describe this embodiment, the device of this embodiment comprises first punch 1, second punch 2, extruding cylinder 3, mandrel 5 and base 6, extruding cylinder 3 is arranged on base 6, and mandrel 5 is located at At the bottom of the extrusion barrel 3, the blank 4 is set in the extrusion barrel 3 and above the mandrel 5, and one end of the first punch 1 and the second punch 2 is set in the extrusion barrel 3 and leans against the blank 4 of the upper end.
specific Embodiment approach 2
[0022] Specific implementation mode two: combination figure 1 Describe this embodiment, the first punch 1 and the second punch 2 of this embodiment are arranged side by side, the height of the first punch 1 and the second punch 2 are the same, the horizontal direction of the first punch 1 and the second punch 2 The cross-section is bow-shaped and the two cross-sections form a circle that matches the extrusion cylinder. The punches are arranged on the left and right to facilitate the alternate downward loading of the two punches, which can reduce the forming load during the extrusion process and reduce the shearing at the interface. Deformation promotes the refinement of grain depth and the improvement of mechanical properties, and the benefits of left and right settings are analyzed. Other implementation manners are the same as the specific implementation manner 1.
specific Embodiment approach 3
[0023] Specific implementation mode three: combination figure 1 To describe this embodiment, the cross-sectional ratio of the first punch 1 and the second punch 2 in this embodiment is 1:1, and the load reduction effect is the most significant in this ratio. Other implementation manners are the same as the specific implementation manner 1.
PUM
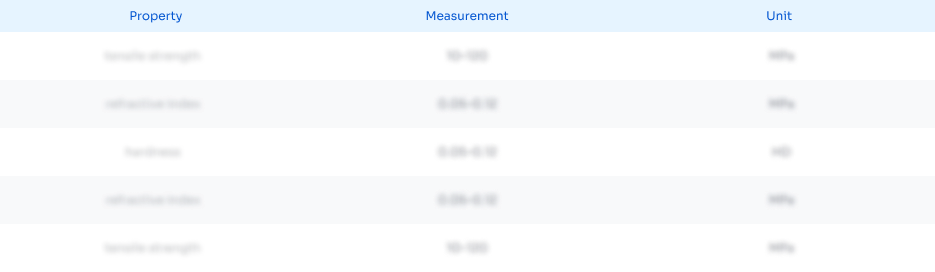
Abstract
Description
Claims
Application Information

- R&D
- Intellectual Property
- Life Sciences
- Materials
- Tech Scout
- Unparalleled Data Quality
- Higher Quality Content
- 60% Fewer Hallucinations
Browse by: Latest US Patents, China's latest patents, Technical Efficacy Thesaurus, Application Domain, Technology Topic, Popular Technical Reports.
© 2025 PatSnap. All rights reserved.Legal|Privacy policy|Modern Slavery Act Transparency Statement|Sitemap|About US| Contact US: help@patsnap.com