Modified complex calcium sulfonate grease and preparation method thereof
A compound calcium sulfonate grease and compound calcium sulfonate technology are applied in lubricating compositions, petroleum industry and other directions, which can solve the problem of poor water drenching resistance and colloidal stability of grease, prolonging production process, reducing production efficiency, etc. problem, to achieve the effect of good shear stability, reduced energy consumption, and good adhesion performance
- Summary
- Abstract
- Description
- Claims
- Application Information
AI Technical Summary
Problems solved by technology
Method used
Image
Examples
preparation example Construction
[0036] One embodiment of the present invention further relates to the preparation method of described high-performance modified composite calcium sulfonate grease, which specifically comprises the following steps:
[0037] (1) Add the base oil and calcium sulfonate with high alkalinity into the clean and sealed reaction kettle according to the proportion of the formula, stir and mix, raise the temperature to 70-90°C, slowly add the conversion agent, keep the addition time not less than 15 minutes, stir Mix evenly and keep warm for no less than 20 minutes;
[0038] (2) After the product in step (1) thickens, heat up to 90-100°C, add calcium hydroxide, dibasic acid, lauryl hydroxystearic acid, and lithium hydroxide, stir and mix evenly, and keep warm for no reaction. less than 40 minutes;
[0039] (3) Then heat up to 120-140°C for dehydration, and keep it for no less than 30 minutes; continue to heat up to 200-220°C for refining, keep the temperature for no less than 3 minutes,...
Embodiment 1
[0045]Add 350g of lubricating base oil (150BS (Jiangyin Xinjiyang Petroleum Sales Co., Ltd.): synthetic oil PAO35 American Texas Petrochemical Company) = 2:1), 330g of high-alkaline synthetic calcium sulfonate into the cleaned and sealed reaction kettle, and stir Mix, heat up to 85°C, slowly add 55g of conversion agent (glacial acetic acid, ethanol, water mass ratio is 3:2:1), stir and react for 25 minutes; continue to heat up to 95°C, add 110g of sebacic acid, 80g Lauryl hydroxystearic acid, 25g calcium hydroxide and 10g lithium hydroxide (diluted three times with hot water), react for 45 minutes; heat up to 140°C for dehydration, keep for 35 minutes; continue to heat up to 220°C for refining, and keep warm for 3 minutes Finally, when the temperature is lowered to 110°C, add 5g of octylbutyldiphenylamine and 35g of palmitic acid, and other antioxidants and modifiers are mixed evenly with the lubricating grease, then cool down to 60°C, grind and homogenize to obtain a finished ...
Embodiment 2
[0047] The proportion of each ingredient is as follows:
[0048] Overbasic Calcium Sulfonate: 330g
[0049] Conversion agent (with embodiment 1): 50g
[0050] Calcium hydroxide: 25g
[0051] Lithium hydroxide: 10g
[0052] Sebacic acid: 100g
[0053] Lauryl hydroxystearic acid: 70g
[0054] Palmitic acid: 30g
[0055] Antioxidant: 5g
[0056] Base oil (same as embodiment 1): 380g
[0057] Modified composite calcium sulfonate grease production process is as embodiment 1, and its performance is as shown in table 1
PUM
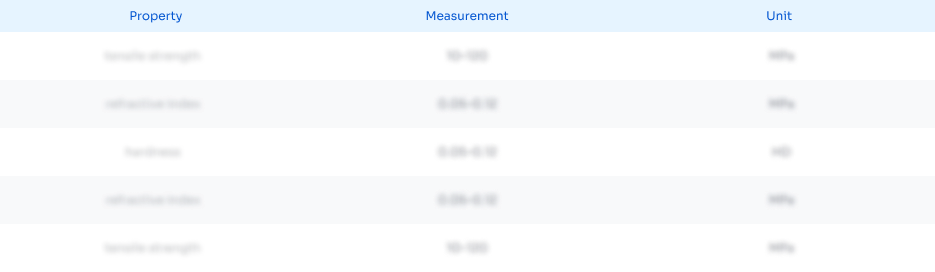
Abstract
Description
Claims
Application Information

- R&D
- Intellectual Property
- Life Sciences
- Materials
- Tech Scout
- Unparalleled Data Quality
- Higher Quality Content
- 60% Fewer Hallucinations
Browse by: Latest US Patents, China's latest patents, Technical Efficacy Thesaurus, Application Domain, Technology Topic, Popular Technical Reports.
© 2025 PatSnap. All rights reserved.Legal|Privacy policy|Modern Slavery Act Transparency Statement|Sitemap|About US| Contact US: help@patsnap.com