Rotary compressor parallel connection system
A compressor and rotor type technology, which is applied in the field of parallel connection system of rotor type compressors, can solve problems such as abnormal wear of the core, large rotor load, and increased input power, and achieve low cost, simple configuration and simple structure.
- Summary
- Abstract
- Description
- Claims
- Application Information
AI Technical Summary
Problems solved by technology
Method used
Image
Examples
Embodiment 1
[0033] Such as figure 1 As shown, a rotary compressor parallel system in a preferred embodiment of the present invention includes a compressor 10 , an oil equalizing pipe 20 , an oil separator 40 and an oil return pipe 50 .
[0034] The compressor 10 of this embodiment is a rotary compressor, which includes a casing 11, a gas-liquid separator 12 connected to the side of the casing 11, and an exhaust pipe 13 arranged on the top of the casing 11. Inside the casing 11 The lower part of the housing 11 is provided with a compression mechanism, which includes a crankshaft, a cylinder 14 and a rolling rotor, and the upper part of the casing 11 is provided with a motor, which includes a rotor and a stator 15 . In the air-conditioning and refrigeration system, the exhaust pipe 13 of the compressor is connected to the oil separator 40 through the high-pressure pipe 30. After the refrigerant is separated from oil and gas by the oil separator 40, the refrigerant passes through the condens...
Embodiment 2
[0058] Such as Figure 7 As shown, the difference between the rotary compressor parallel system of this embodiment and the first embodiment is that the oil outlet 22 of the oil equalizing pipe of this embodiment and the high-pressure piping 30 connecting the exhaust pipe 13 and the oil separator 40 It is different from the way in which the oil outlet 22 of the oil equalizing pipe is directly connected to the exhaust pipe 13 in the first embodiment. When manufacturing the compressor, it is not necessary to weld the oil equalizing pipe 20 on the exhaust pipe 13. Instead, the oil equalizing pipe joint is reserved on the high-pressure piping 30, and the oil outlet 22 of the oil equalizing pipe is installed on the oil equalizing pipe joint of the high-pressure piping 30 when the entire compressor is assembled. The installation of the oil equalizing pipe 20 in this embodiment The structure can reduce the difficulty of manufacturing the compressor.
[0059] Since the high-pressure p...
PUM
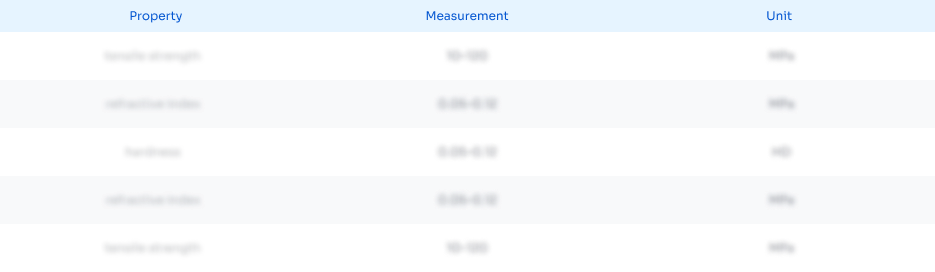
Abstract
Description
Claims
Application Information

- Generate Ideas
- Intellectual Property
- Life Sciences
- Materials
- Tech Scout
- Unparalleled Data Quality
- Higher Quality Content
- 60% Fewer Hallucinations
Browse by: Latest US Patents, China's latest patents, Technical Efficacy Thesaurus, Application Domain, Technology Topic, Popular Technical Reports.
© 2025 PatSnap. All rights reserved.Legal|Privacy policy|Modern Slavery Act Transparency Statement|Sitemap|About US| Contact US: help@patsnap.com