Plastic rib spiral pipe without adhesive-bonded joints and manufacturing technique thereof
A plastic rib spiral and production process technology, applied in the field of plastic rib pipe production equipment, can solve the problems of weak bonding of joints, increased scrap rate, inability to produce small-diameter pipes, etc., and achieve smooth transportation, product quality improvement, and transportation. and no residual effect
- Summary
- Abstract
- Description
- Claims
- Application Information
AI Technical Summary
Problems solved by technology
Method used
Image
Examples
Embodiment Construction
[0010] The present invention will be further described below in conjunction with the accompanying drawings and embodiments.
[0011] Such as figure 1 As shown, the plastic-reinforced spiral pipe without bonding seam includes a plastic-reinforced pipe body 11, an inner smooth surface 12 formed integrally with the inner wall of the plastic-reinforced pipe body 11, and an integrated outer wall of the plastic-reinforced pipe body 11. The formed outer smooth surface 13 and the outer wall of the plastic rib tube body 11 are provided with spiral plastic ribs 14 wound on the tube body.
[0012] The production process of the plastic-reinforced spiral pipe without adhesive joints includes the following steps. The plastic-reinforced pipe material is extruded from the extruder head, and the plastic-reinforced pipe body 11 is formed in the plastic-reinforced pipe forming channel. At the same time, the spiral plastic-reinforced material After entering from the helical material injection ch...
PUM
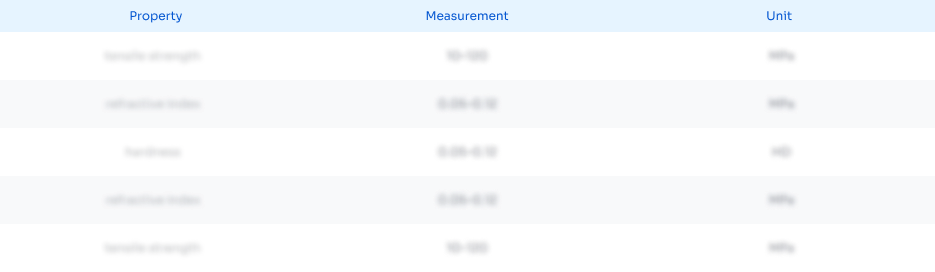
Abstract
Description
Claims
Application Information

- Generate Ideas
- Intellectual Property
- Life Sciences
- Materials
- Tech Scout
- Unparalleled Data Quality
- Higher Quality Content
- 60% Fewer Hallucinations
Browse by: Latest US Patents, China's latest patents, Technical Efficacy Thesaurus, Application Domain, Technology Topic, Popular Technical Reports.
© 2025 PatSnap. All rights reserved.Legal|Privacy policy|Modern Slavery Act Transparency Statement|Sitemap|About US| Contact US: help@patsnap.com