A self-unloading device for materials
A self-unloading device and material technology, applied in the field of machinery, can solve the problems of unfavorable production efficiency, increase the use cost of machinery and labor cost, waste energy, etc., and achieve the effect of saving energy, saving time and improving efficiency.
- Summary
- Abstract
- Description
- Claims
- Application Information
AI Technical Summary
Problems solved by technology
Method used
Image
Examples
Embodiment 1
[0029] Such as figure 1 and figure 2 As shown, a material self-unloading device that swings through the elasticity and gravity of the tension spring includes a fixed plate 4, a rotating shaft 5, a material plate 6, a first tension spring 8, a second tension spring 9 and a spring connection Plate 2, wherein one end of the material plate 6 is fixedly connected to the rotating shaft 5, the upper surface of the material plate 6 is set as a rough surface, and the purpose of setting the upper surface of the material plate 6 as a rough surface is to ensure that the material plate 6 and the material are tilted and in a critical position. At this point, the material will not slide down so that it cannot break through the critical point. Specifically, the critical angle of the material plate is determined by the friction coefficient between the material and the material plate, and the critical angle should be smaller than the self-locking angle between the material and the material pl...
Embodiment 2
[0032] This embodiment is the same as Embodiment 1 except for the following features.
[0033] The spring connecting plate 2 is arranged on the rotating shaft 5, and can also be arranged on the right side of the rotating shaft 5 according to the installation situation of the material self-unloading device. The spring connecting plate 2 is arranged in a circular shape. One end of the material plate 6 is fixedly connected to the rotating shaft 5, and the upper surface of the material plate 6 is a granular rough surface.
Embodiment 3
[0035] This embodiment is the same as Embodiment 1 except for the following features.
[0036] The spring connecting plate 2 is arranged on the rotating shaft 5, and can also be arranged in the middle of the rotating shaft 5 according to the installation situation of the material self-unloading device. The spring connecting plate 2 is arranged in a square shape. One end of the material plate 6 is fixedly connected to the rotating shaft 5, and the upper surface of the material plate 6 is a striped rough surface.
PUM
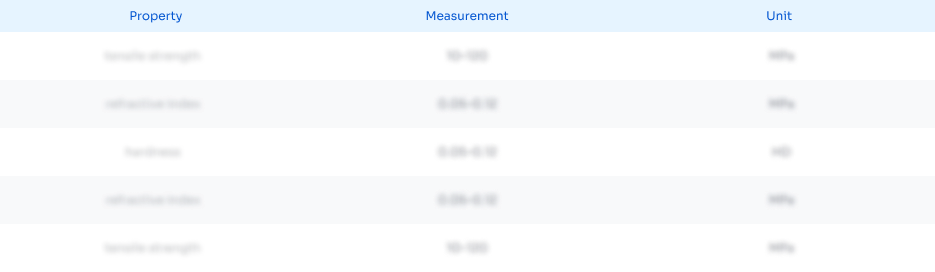
Abstract
Description
Claims
Application Information

- Generate Ideas
- Intellectual Property
- Life Sciences
- Materials
- Tech Scout
- Unparalleled Data Quality
- Higher Quality Content
- 60% Fewer Hallucinations
Browse by: Latest US Patents, China's latest patents, Technical Efficacy Thesaurus, Application Domain, Technology Topic, Popular Technical Reports.
© 2025 PatSnap. All rights reserved.Legal|Privacy policy|Modern Slavery Act Transparency Statement|Sitemap|About US| Contact US: help@patsnap.com