CAE (computer aided engineering)-based car body rigidity analysis method
A technology of stiffness analysis and body, applied in the field of body stiffness analysis based on CAE, which can solve the problems of poor compatibility of processing results, inconvenient measurement results, and high cost of body stiffness analysis methods
- Summary
- Abstract
- Description
- Claims
- Application Information
AI Technical Summary
Problems solved by technology
Method used
Image
Examples
Embodiment Construction
[0028] The following will clearly and completely describe the technical solutions in the embodiments of the present invention with reference to the accompanying drawings in the embodiments of the present invention. Obviously, the described embodiments are only some of the embodiments of the present invention, not all of them. Based on the embodiments of the present invention, all other embodiments obtained by persons of ordinary skill in the art without making creative efforts belong to the protection scope of the present invention.
[0029] see figure 1 As shown in the flow chart, this embodiment provides a CAE-based vehicle body stiffness analysis method based on the secondary development interface provided by MSC / NASTRAN software and HyperWorks software, based on the TCL (Tool Command Language) language, for analyzing the bending of the vehicle body Stiffness and torsional stiffness, including:
[0030] Step 101: Establish a finite element grid model of the vehicle body, a...
PUM
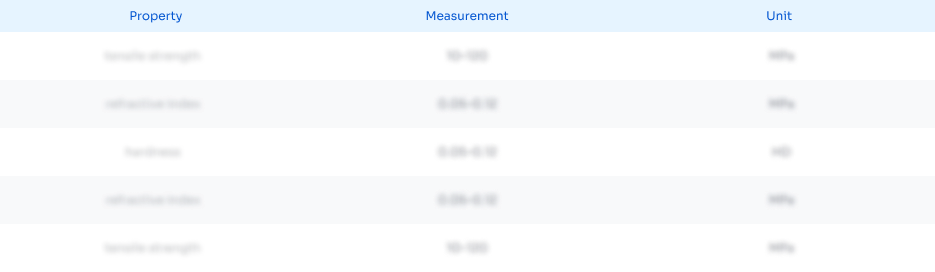
Abstract
Description
Claims
Application Information

- Generate Ideas
- Intellectual Property
- Life Sciences
- Materials
- Tech Scout
- Unparalleled Data Quality
- Higher Quality Content
- 60% Fewer Hallucinations
Browse by: Latest US Patents, China's latest patents, Technical Efficacy Thesaurus, Application Domain, Technology Topic, Popular Technical Reports.
© 2025 PatSnap. All rights reserved.Legal|Privacy policy|Modern Slavery Act Transparency Statement|Sitemap|About US| Contact US: help@patsnap.com