Spun-bonded non-woven fabric with function of preventing diaper rashes
A spunbonded non-woven fabric and diaper rash technology, which is applied in the field of spunbonded nonwoven fabrics, can solve problems such as limiting moisture volatilization, local poor ventilation, and inability to effectively prevent diaper rash.
- Summary
- Abstract
- Description
- Claims
- Application Information
AI Technical Summary
Problems solved by technology
Method used
Image
Examples
Embodiment 1
[0023] The preparation of the finishing agent: Put 46kg of deionized water in a conventional liquid washing pot, heat to 70°C, start stirring, the stirring speed is 100 rpm, and 18kg of cetearyl ether-20, 10kg are sequentially added during stirring. Didecyl dimethyl ammonium chloride (active substance content 70%), 12kg laureth-9, 6kg sucrose octasulfate, 3kg bisabolol, 2kg pentanediol, 3kg 1,3-propanediol; Maintain 70°C and continue stirring for 30 minutes to fully dissolve all materials; turn on cooling water, cool to normal temperature; discharge.
[0024] The finishing of the spunbonded non-woven fabric: the finishing is implemented using non-woven fabric padding, drying finishing equipment and technological processes known in the art. Add 98 kilograms of deionized water and 2 kilograms of the finishing agent into a conventional batcher, stir and mix uniformly under normal temperature conditions to make a diluted finishing agent. The spunbond non-woven fabric weighing 20 gra...
Embodiment 2
[0025] Example 2. Finishing of the spunbond non-woven fabric
[0026] The finishing is implemented using non-woven padding, drying finishing equipment and technological processes known in the art. Add 98 kilograms of deionized water and 2 kilograms of the finishing agent into a conventional batcher, stir and mix uniformly under normal temperature conditions to make a diluted finishing agent. The spunbond non-woven fabric weighing 25 grams per square gram is finished with the diluted finishing agent. The specific process parameters are: linear speed 80 m / min; one dipping and one rolling; the roller spacing is set to 0.25 mm, so that the adsorption amount of the diluted finishing agent on the spunbonded non-woven fabric is nothing by weight percentage. 20±1% of the weight of the woven fabric; dried at 125℃.
Embodiment 3
[0027] Example 3. Three kinds of surfactants synergy experiment (three-factor three-level orthogonal experiment)
[0028] According to the preliminary test results, the design level factor table is shown in Table 1.
[0029] Table 1. Level factor table
[0030]
[0031] The finishing agent formula is designed according to the above-mentioned level factor table, and the dosages of the three surfactants are respectively set. The other components except deionized water and their dosages remain unchanged, and the deionized water is added to 100%; according to Example 2 According to the method shown, 9 groups of finished spunbond non-woven fabrics were obtained, and the first penetration time, the fifth penetration time and the longitudinal softness were measured respectively, and the corresponding orthogonal test data was calculated.
[0032] 1. Results and analysis of orthogonal test for the first penetration time:
[0033] Table 2. Results of orthogonal test for the first penetration ti...
PUM
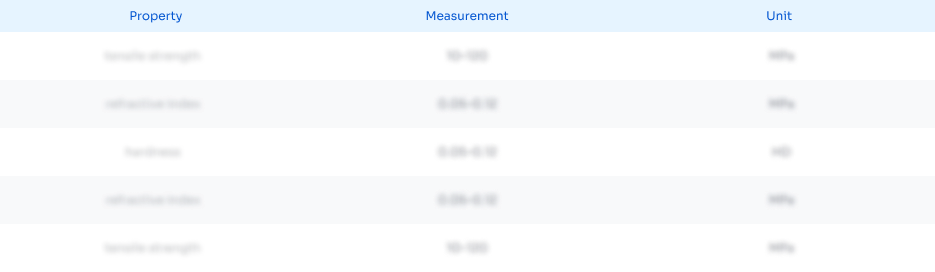
Abstract
Description
Claims
Application Information

- Generate Ideas
- Intellectual Property
- Life Sciences
- Materials
- Tech Scout
- Unparalleled Data Quality
- Higher Quality Content
- 60% Fewer Hallucinations
Browse by: Latest US Patents, China's latest patents, Technical Efficacy Thesaurus, Application Domain, Technology Topic, Popular Technical Reports.
© 2025 PatSnap. All rights reserved.Legal|Privacy policy|Modern Slavery Act Transparency Statement|Sitemap|About US| Contact US: help@patsnap.com