A vertical coating fixture
A vertical placement and fixture technology, used in sputtering, ion implantation, vacuum evaporation, etc., can solve problems such as poor mirror surface shape accuracy, and achieve the effect of easy installation and simple operation
- Summary
- Abstract
- Description
- Claims
- Application Information
AI Technical Summary
Problems solved by technology
Method used
Image
Examples
example example 1
[0021] A kind of vertically placed coating fixture of this embodiment, such as Figure 1a , 1b , Figure 2 ~ Figure 6 shown.
[0022] All components of this embodiment such as figure 2 shown. The object to be coated is mirror 1, such as image 3 As shown, its structure is a hollow structure with poor rigidity. The fixture main body 2 is a ring-shaped shell, and the reflector 1 is placed in the inner cavity of the fixture main body 2. There are three arc-shaped cushion blocks 5 uniformly distributed at 120° on the inner surface of the fixture main body 2, and the outer circle of the arc-shaped cushion block 5 The arc surface 502 matches the three inner cavity contours 205 of the clamp body 2 , and the inner arc surface 501 matches the outer diameter contour of the mirror 1 . There are 6 jacking screws 3 radially distributed on the side part of the main body of the fixture, which are used to adjust the gap between the arc-shaped pad 5 and the reflector 1 to clamp the refle...
PUM
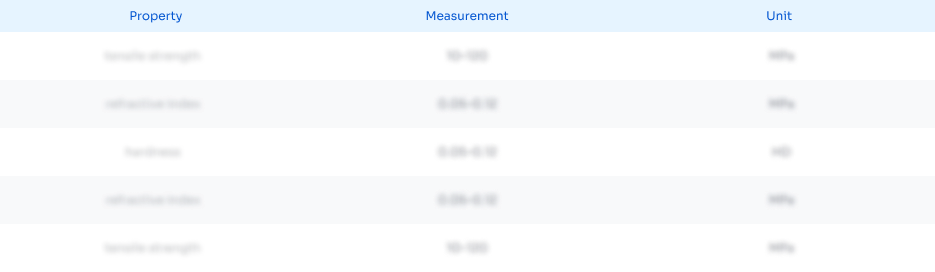
Abstract
Description
Claims
Application Information

- R&D
- Intellectual Property
- Life Sciences
- Materials
- Tech Scout
- Unparalleled Data Quality
- Higher Quality Content
- 60% Fewer Hallucinations
Browse by: Latest US Patents, China's latest patents, Technical Efficacy Thesaurus, Application Domain, Technology Topic, Popular Technical Reports.
© 2025 PatSnap. All rights reserved.Legal|Privacy policy|Modern Slavery Act Transparency Statement|Sitemap|About US| Contact US: help@patsnap.com