Push rod mechanism of metal die-casting mold
A push rod mechanism and die-casting die technology, applied in the field of metal die-casting, can solve the problems of sticking together, unable to achieve rapid push-out, etc., and achieve the effects of easy processing and maintenance, safe and reliable push-out action, and improved service life.
- Summary
- Abstract
- Description
- Claims
- Application Information
AI Technical Summary
Problems solved by technology
Method used
Image
Examples
Embodiment Construction
[0013] In order to make the object, technical solution and advantages of the present invention clearer, the present invention will be further described in detail below in conjunction with the accompanying drawings and embodiments. It should be understood that the specific embodiments described here are only used to explain the present invention, not to limit the present invention.
[0014] see figure 1 , figure 1 It is a structural schematic diagram of the present invention.
[0015] The push rod mechanism of a metal die-casting mold includes a support plate 1, a movable template 2, a push rod 3, and a die casting 6. The movable template 2 is installed above the support plate 1, and between the support plate 1 and the movable template 2 A concentric installation hole is opened on the top, the push rod 3 passes through the installation hole and contacts the bottom end of the die casting 6, one side of the push rod 3 is connected with the plastic guide sleeve layer 7, and the ...
PUM
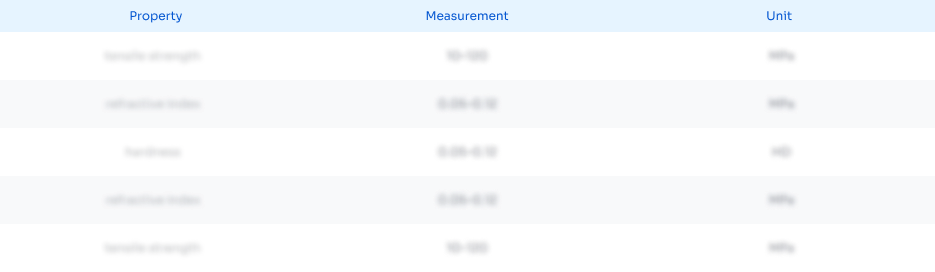
Abstract
Description
Claims
Application Information

- R&D Engineer
- R&D Manager
- IP Professional
- Industry Leading Data Capabilities
- Powerful AI technology
- Patent DNA Extraction
Browse by: Latest US Patents, China's latest patents, Technical Efficacy Thesaurus, Application Domain, Technology Topic, Popular Technical Reports.
© 2024 PatSnap. All rights reserved.Legal|Privacy policy|Modern Slavery Act Transparency Statement|Sitemap|About US| Contact US: help@patsnap.com