On-line abrasive particle monitoring method and monitoring sensor based on bilateral symmetric structure of the radial magnetic field
A technology for monitoring sensors and radial magnetic fields, applied in instruments, analytical materials, etc., can solve the problems of easy damage of lubricating oil film, affecting detection sensitivity, total magnetic flux loss, etc., and achieve the effect of improving magnetic flux, improving sensitivity, and improving accuracy
- Summary
- Abstract
- Description
- Claims
- Application Information
AI Technical Summary
Problems solved by technology
Method used
Image
Examples
Embodiment Construction
[0045] The present invention will be further described below in conjunction with the drawings.
[0046] The invention is based on the radial magnetic field-based on-line wear particle monitoring method of bilateral symmetric structure, such as figure 2 As shown, it is implemented in the following way:
[0047] First, apply mutually symmetrical magnetic fields with opposite rotation directions to the symmetrical positions on both sides of the oil pipe of the oil equipment to form a bilateral symmetrical magnetic field loop as the excitation source; at this time, the two magnetic fields are superimposed at the oil pipe and act on the oil pipe in the radial direction. ; Next, when abrasive particles in the tubing pass through the magnetic field loop, it will cause the magnetic flux of the magnetic field loop to change. The change of magnetic flux will cause the voltage in the detection coil to change, and the detection coil will output its own induced voltage signal u in real time:
[...
PUM
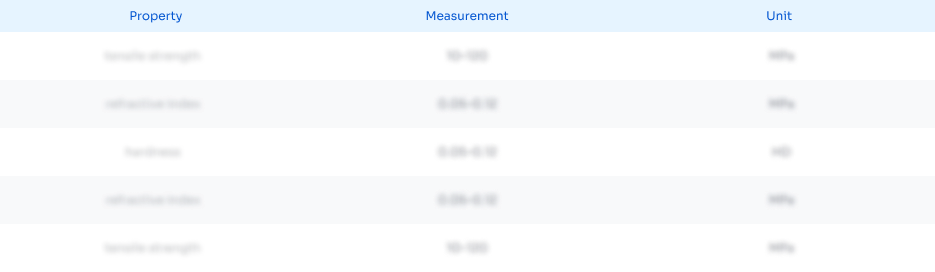
Abstract
Description
Claims
Application Information

- R&D
- Intellectual Property
- Life Sciences
- Materials
- Tech Scout
- Unparalleled Data Quality
- Higher Quality Content
- 60% Fewer Hallucinations
Browse by: Latest US Patents, China's latest patents, Technical Efficacy Thesaurus, Application Domain, Technology Topic, Popular Technical Reports.
© 2025 PatSnap. All rights reserved.Legal|Privacy policy|Modern Slavery Act Transparency Statement|Sitemap|About US| Contact US: help@patsnap.com