Chuck gripper device of stacking robot for complex surface
A technology for stacking robots and complex surfaces, which is applied in the field of suction cup gripper devices for stacking robots, to achieve the effects of avoiding material leakage and loss, ensuring stability and reliability of grasping, and flexible operation
- Summary
- Abstract
- Description
- Claims
- Application Information
AI Technical Summary
Problems solved by technology
Method used
Image
Examples
Embodiment Construction
[0028] Such as Figure 1 to Figure 3 As shown, the present invention is a stacking robot sucker gripper device for complex surfaces, including a connecting flange 1, a mounting frame 2, a lateral adjustment mechanism 3, a longitudinal adjustment mechanism 4, an adsorption mechanism 5, a man-machine control interface and an electrical protective device;
[0029] The described lateral adjustment mechanism 3 includes a lateral drive motor 6, a double-rotation lead screw 10, a laterally movable slider 7, a slider connecting plate 8, and a laterally supporting rail 9; the laterally moving slider 7 is arranged on the laterally supporting rail 9 Above, the laterally moving slider 7 is connected to the slider connecting plate 8, the double-rotation lead screw 10 is located at the center of the lateral adjustment mechanism 4, and the drive motor 6 is arranged at one end of the lateral adjustment mechanism 4 and the double-rotation direction Leading screw 10 links to each other;
[00...
PUM
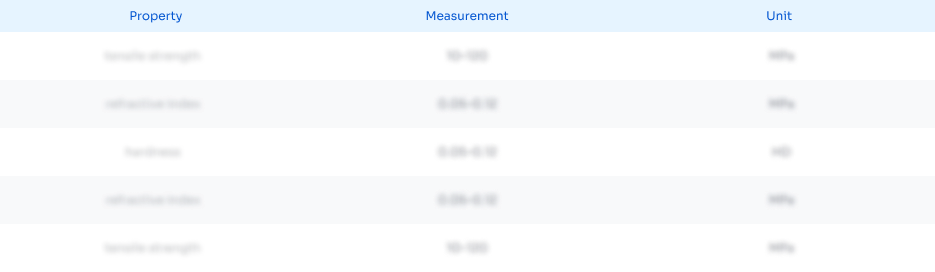
Abstract
Description
Claims
Application Information

- R&D
- Intellectual Property
- Life Sciences
- Materials
- Tech Scout
- Unparalleled Data Quality
- Higher Quality Content
- 60% Fewer Hallucinations
Browse by: Latest US Patents, China's latest patents, Technical Efficacy Thesaurus, Application Domain, Technology Topic, Popular Technical Reports.
© 2025 PatSnap. All rights reserved.Legal|Privacy policy|Modern Slavery Act Transparency Statement|Sitemap|About US| Contact US: help@patsnap.com