Pull rod machining technology
A processing technology and tie rod technology, applied in the field of tie rod processing technology, can solve the problems of insufficient tie rod strength, unfavorable production, insufficient tie rod hole accuracy, etc., and achieve the effects of reducing production cost, reducing defective rate and improving accuracy.
- Summary
- Abstract
- Description
- Claims
- Application Information
AI Technical Summary
Problems solved by technology
Method used
Image
Examples
Embodiment 2
[0012] Embodiment 2: the first step: cut the material with a laser cutting machine, and initially cut out the shape of the product according to the size of the drawing, which is L-shaped, 185mm long, 95mm wide, and 23mm thick, and the shape of the product is initially determined; Step 2: Use a milling machine to perform positioning processing on the cut product, and drill a round hole at a distance of 21.5mm from the bottom of the product and 22.5mm on the side, with a diameter of φ25mm, and perform positioning processing according to the requirements of the drawing; Step 3: Mill the hole with a milling machine , and the upper end of the φ25mm round hole, drill a φ10mm round hole at a distance of 60mm, and process according to the drawing; the fourth step: use a milling machine to further process the material, and on the material at a center distance of 143.5mm from the φ25mm round hole For processing, mill R20 arcs on the upper and lower ends of the surface, the length is 20mm...
Embodiment 3
[0013] Embodiment three: the first step: cut the material with a laser cutting machine, and initially cut out the shape of the product according to the size of the drawing, which is L-shaped, 185mm long, 95mm wide, and 23mm thick, and the shape of the product is initially determined; Step 2: Use a milling machine to perform positioning processing on the cut product, and drill a round hole at a distance of 21.5mm from the bottom of the product and 22.5mm on the side, with a diameter of φ25.2mm, and perform positioning processing according to the drawing requirements; Step 3: Use a milling machine Mill the hole, drill the upper end of the φ25.2mm round hole, drill the φ10.18mm round hole at the middle distance of 60.2mm, and process it according to the drawing; the fourth step: use a milling machine to further process the material, and drill the φ25.2mm round hole The material at the center distance of 143.5mm is processed, and the surface of the upper and lower ends is milled wi...
PUM
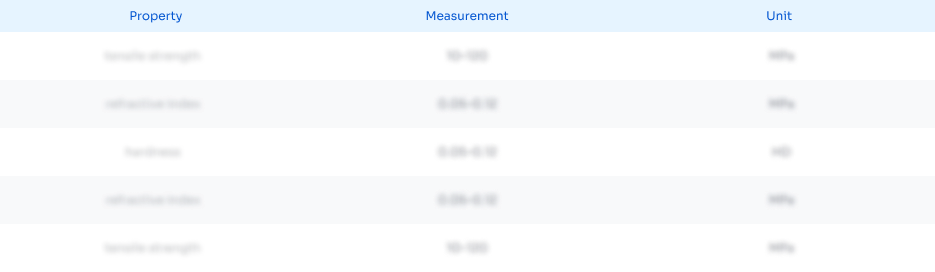
Abstract
Description
Claims
Application Information

- R&D Engineer
- R&D Manager
- IP Professional
- Industry Leading Data Capabilities
- Powerful AI technology
- Patent DNA Extraction
Browse by: Latest US Patents, China's latest patents, Technical Efficacy Thesaurus, Application Domain, Technology Topic, Popular Technical Reports.
© 2024 PatSnap. All rights reserved.Legal|Privacy policy|Modern Slavery Act Transparency Statement|Sitemap|About US| Contact US: help@patsnap.com