Five-axis cutter radius compensation method based on post-processing
A tool radius and post-processing technology, which is applied in the direction of instruments, computer control, simulators, etc., can solve the problem of tool length compensation without five-axis tools
- Summary
- Abstract
- Description
- Claims
- Application Information
AI Technical Summary
Problems solved by technology
Method used
Image
Examples
Embodiment Construction
[0023] The preferred embodiment of the five-axis tool length compensation method based on post-processing of the present invention includes:
[0024] A. The basic principle of five-axis tool radius compensation has been studied, and the vectors for the direction of tool radius compensation and the compensation position of the rear tool have been deduced for three commonly used end mills, such as ball nose cutters, flat bottom cutters and ring cutters. equation;
[0025] In the process of five-axis end milling to process curved surfaces, commonly used tool types include ball-end cutters, flat-bottomed cutters, and ring cutters. In order to study the basic principles of five-axis tool radius compensation, the radius compensation directions for the above three types of tools will be deduced below. And compensated flank point vector equation.
[0026] 1. Ball nose cutter radius compensation direction and compensation rear cutter position vector
[0027] Such as figure 1 as show...
PUM
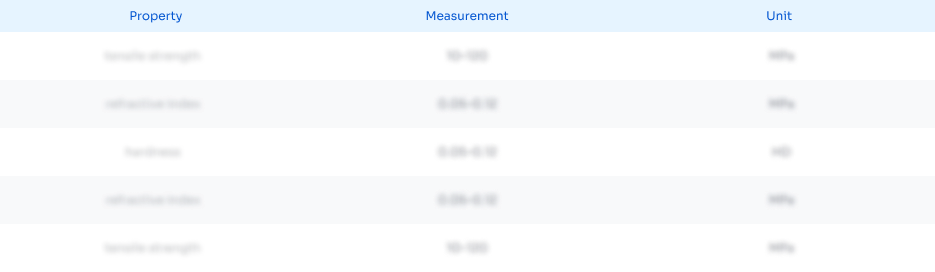
Abstract
Description
Claims
Application Information

- R&D Engineer
- R&D Manager
- IP Professional
- Industry Leading Data Capabilities
- Powerful AI technology
- Patent DNA Extraction
Browse by: Latest US Patents, China's latest patents, Technical Efficacy Thesaurus, Application Domain, Technology Topic, Popular Technical Reports.
© 2024 PatSnap. All rights reserved.Legal|Privacy policy|Modern Slavery Act Transparency Statement|Sitemap|About US| Contact US: help@patsnap.com