Metal plate support structure for being assembled with plastic part and assembling method thereof
A technology for sheet metal brackets and plastic parts, which is applied in the direction of connecting members, shrinking connections, mechanical equipment, etc., can solve the problems of difficult operation and easily damaged workpieces, and achieve the effects of simple processing technology, guaranteed strength and low processing cost.
- Summary
- Abstract
- Description
- Claims
- Application Information
AI Technical Summary
Problems solved by technology
Method used
Image
Examples
Embodiment Construction
[0024] like Figure 1 ~ Figure 3 A sheet metal bracket structure for assembling with plastic parts is shown, including a support plate 1, a through hole 2 is provided on the support plate 1, and two slots for inserting the end of the support plate 1 are provided on the plastic part, The plastic part is provided with a buckle 3 placed in the through hole 2, and the support plate 1 protrudes with a bump 4 placed between the two slots of the plastic part. The bump 4 protrudes toward the through hole 2 and has a folded section Curved elastic buckle. In the assembled state of the plastic part and the sheet metal bracket, the end of the elastic buckle bears against the buckle 3 of the plastic part. Both sides of the support plate 1 are respectively provided with a plurality of assembly bosses 5 which are snapped into the slots on the plastic parts.
[0025] The elastic buckle includes a first connecting plate 6 , a second connecting plate 7 and a third connecting plate 8 which are...
PUM
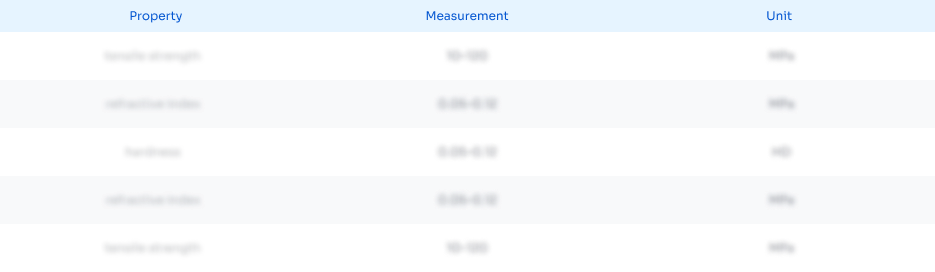
Abstract
Description
Claims
Application Information

- R&D
- Intellectual Property
- Life Sciences
- Materials
- Tech Scout
- Unparalleled Data Quality
- Higher Quality Content
- 60% Fewer Hallucinations
Browse by: Latest US Patents, China's latest patents, Technical Efficacy Thesaurus, Application Domain, Technology Topic, Popular Technical Reports.
© 2025 PatSnap. All rights reserved.Legal|Privacy policy|Modern Slavery Act Transparency Statement|Sitemap|About US| Contact US: help@patsnap.com