A bridge deck crane structure
A technology for cranes and main structures, applied in bridges, bridge construction, erection/assembly of bridges, etc., can solve the problems of affecting the shape of the structure and force, waste, and dismantling after one use
- Summary
- Abstract
- Description
- Claims
- Application Information
AI Technical Summary
Problems solved by technology
Method used
Image
Examples
Embodiment Construction
[0023] The present invention will be further described below in conjunction with the embodiments shown in the accompanying drawings.
[0024] Such as figure 1 As shown, the present invention discloses a bridge deck crane structure, including a crane main structure 1, a length-adjustable connecting truss 11, an oil cylinder adjustment system and a computer control system, wherein the crane main structure is two sets of space trusses or Rigid frame steel structure, space truss or steel members in the rigid frame steel structure are connected by high-strength bolts or welding, and two sets of space truss or rigid frame steel structures are connected via the connecting truss in the direction of the bridge (that is, the X direction in the figure). 11 for connection. When assembling on site, first assemble the main structure 1 of the crane, then adjust the number of connecting trusses 11 according to the actual situation on site, and finally connect the connecting trusses 11 to two ...
PUM
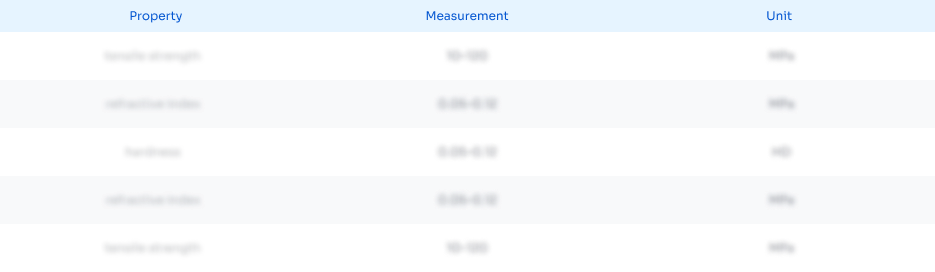
Abstract
Description
Claims
Application Information

- R&D Engineer
- R&D Manager
- IP Professional
- Industry Leading Data Capabilities
- Powerful AI technology
- Patent DNA Extraction
Browse by: Latest US Patents, China's latest patents, Technical Efficacy Thesaurus, Application Domain, Technology Topic, Popular Technical Reports.
© 2024 PatSnap. All rights reserved.Legal|Privacy policy|Modern Slavery Act Transparency Statement|Sitemap|About US| Contact US: help@patsnap.com