A kind of anthracite lime kiln which adopts the fire bar combustion method to continuously add combustion materials
A combustion method and lime kiln technology, applied in the field of lime kiln equipment, can solve the problems of increased cost, low output of quicklime, inability to achieve energy saving and environmental protection, etc., and achieve the effect of improving production efficiency and reducing dosage.
- Summary
- Abstract
- Description
- Claims
- Application Information
AI Technical Summary
Problems solved by technology
Method used
Image
Examples
Embodiment 1
[0063] combine figure 2 and image 3 as shown,
[0064] The furnace wall 2021 in this embodiment is composed of two refractory brick wall panels formed into an inverted V shape, and the bottom ends of the two refractory brick wall panels forming an inverted V shape are connected to the two ends of the fire grate 2022 respectively. connected into one body so that the furnace 202 is formed into a Mitsubishi columnar structure; A small hole through which the flames of the burning material inside are ejected.
[0065] In this way, when the limestone material is calcined by the present invention, two refractory brick wall panels formed into an inverted V shape are used as the furnace wall 2021 of the furnace 202. On the one hand, the combustibles in the furnace 202 are burned The flame can be ejected from the small hole on the refractory brick wallboard to calcine the corresponding limestone material. On the other hand, the limestone material in the cylindrical furnace body 10 ...
Embodiment 2
[0067] combine Figure 4 and Figure 5 shown;
[0068] The furnace wall 2021 in this embodiment is composed of two inverted V-shaped refractory furnace bars provided with stepped water circulation flat iron pipes 209, and the bottom ends of the two refractory furnace bars forming an inverted V shape are respectively connected to The two ends of the fire grate 2022 are integrated so that the furnace 202 is formed into a Mitsubishi columnar structure; The lower end of the outer side of the bar is inclined, and the inside of the stepped water circulation flat iron pipe 209 is connected. A water outlet, the water outlet is connected with a water outlet pipe 210, and the water outlet pipe 210 penetrates to the outside of the furnace body base 20; there is a water outlet between the adjacent water circulation flat iron pipes 209 to make the combustion in the furnace 202 The gap where the flames of burning objects are ejected.
[0069]In this way, when the limestone material is c...
Embodiment 3
[0071] combine Figure 6 and Figure 7 shown;
[0072] The furnace wall 2021 in this embodiment is made of a conical refractory brick wall, and the bottom end of the conical refractory brick wall is integrated with the fire grate 2022, so that the furnace 202 It is formed into a three-dimensional conical structure; and the conical refractory brick wall surface is provided with a plurality of flames inclined to the outer lower end of the conical refractory brick wall surface so that the combustibles in the furnace 202 can be burned Jetted holes.
[0073] In this way, when the limestone material is calcined by the present invention, the conical refractory brick wall is used as the furnace wall 2021 of the furnace 202. On the one hand, the flame burned by the combustibles in the furnace 202 can be The corresponding limestone materials are sprayed out from the small holes on the wall of the refractory bricks. On the other hand, the limestone materials in the cylindrical furnace...
PUM
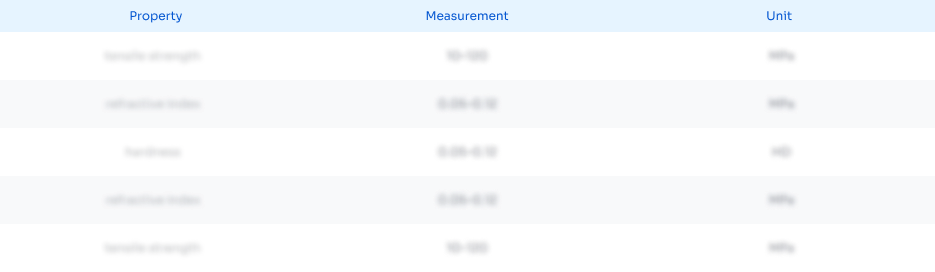
Abstract
Description
Claims
Application Information

- R&D
- Intellectual Property
- Life Sciences
- Materials
- Tech Scout
- Unparalleled Data Quality
- Higher Quality Content
- 60% Fewer Hallucinations
Browse by: Latest US Patents, China's latest patents, Technical Efficacy Thesaurus, Application Domain, Technology Topic, Popular Technical Reports.
© 2025 PatSnap. All rights reserved.Legal|Privacy policy|Modern Slavery Act Transparency Statement|Sitemap|About US| Contact US: help@patsnap.com