Skylight lateral shaping die
A side shaping and skylight technology, applied in the direction of forming tools, manufacturing tools, metal processing equipment, etc., can solve the problems of increasing maintenance costs and product quality risks, high mold manufacturing costs, reducing production efficiency, etc., to eliminate the scrapped parts. and the risk of mold damage, the effect of reducing mold development costs and reducing maintenance costs
- Summary
- Abstract
- Description
- Claims
- Application Information
AI Technical Summary
Problems solved by technology
Method used
Image
Examples
Embodiment 1
[0016] Such as image 3 , 4 As shown, as a preferred embodiment of the present invention, the first insert 11 is fixedly installed on the front end of the push rod 30, and the left and right sides of the push rod 30 are equipped with The oblique wedges 31 , 32 pressed against the flanges 412 , 413 on both sides of the skylight 41 constitute the transmission unit.
[0017] Further, the second and third inserts 12 and 13 are respectively provided with backing plates parallel to the slopes of the oblique wedges 31 and 32 , and the backing plates and the oblique wedges 31 and 32 form an inclined plane transmission fit.
Embodiment 2
[0019] Such as Figure 5 As shown, the first insert 11 is fixedly installed on the front end of the push rod 30, and a horizontally arranged connecting rod 33, 34 is respectively provided between the push rod 30 and the second and third inserts 12, 13, so that The connecting rods 33, 34 are hingedly connected to the push rod 30, the second and third inserts 12, 13, and the axes of the hinged shafts are arranged along the vertical direction.
[0020] As a preferred technical solution of the present invention, the lower mold base is also provided with elastic units for driving the first, second and third inserts 11, 12, 13 to reset, and the elastic units include corresponding The first, second and third inserts 11, 12 and 13 are provided with three compression springs or gas springs.
[0021] Further, the lower mold base is also provided with a limit block 14 for limiting the limit position of the push rod 30, the limit block 14 is located on both sides of the push rod 30, and ...
PUM
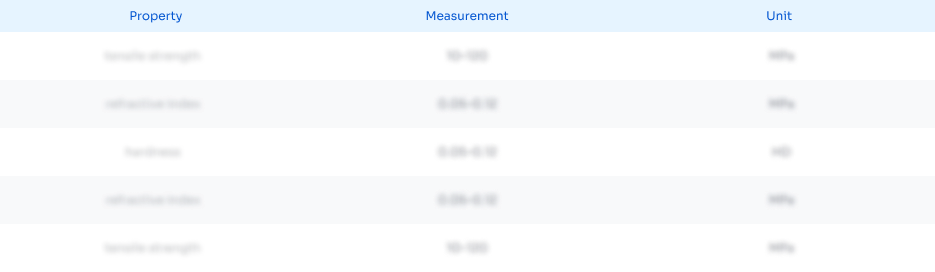
Abstract
Description
Claims
Application Information

- Generate Ideas
- Intellectual Property
- Life Sciences
- Materials
- Tech Scout
- Unparalleled Data Quality
- Higher Quality Content
- 60% Fewer Hallucinations
Browse by: Latest US Patents, China's latest patents, Technical Efficacy Thesaurus, Application Domain, Technology Topic, Popular Technical Reports.
© 2025 PatSnap. All rights reserved.Legal|Privacy policy|Modern Slavery Act Transparency Statement|Sitemap|About US| Contact US: help@patsnap.com