A pouring system for a wheel hub
A pouring system and wheel hub technology, applied in casting molding equipment, casting molds, cores, etc., can solve problems such as shrinkage cavity/loose defects, and achieve the effects of ensuring integrity, eliminating pouring defects, and overcoming pouring defects
- Summary
- Abstract
- Description
- Claims
- Application Information
AI Technical Summary
Problems solved by technology
Method used
Image
Examples
Embodiment Construction
[0019] The present invention as figure 2 shown.
[0020] A pouring system for a wheel hub. The outer structure of the wheel hub is divided into a first step 1, a second step 2, a flange 3 and a straight cylinder 4 in sequence, and the interior is provided with a bearing installation position 5, and the flange 3 is provided with a mounting groove. 6. A feeding riser 7 is provided on the outer circle of the second step 2, and the feeding riser 7 is connected to the sprue 9 through the runner 8.
[0021] There is a distance between the 7 roots of the feeding riser and the 3 flanges, and the distance is 3-5mm.
[0022] Fractures 10 are also provided on the root of the feeding riser 7 and the second step 2 .
PUM
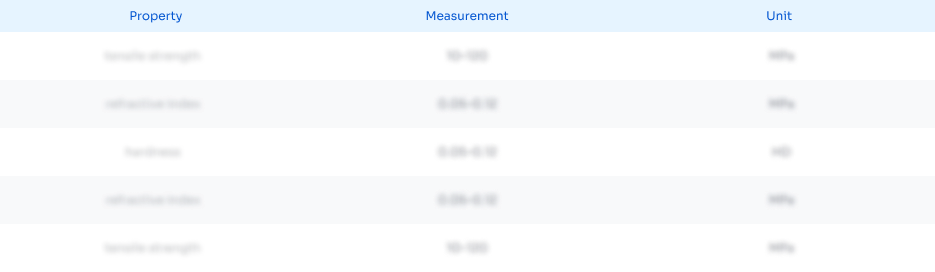
Abstract
Description
Claims
Application Information

- R&D
- Intellectual Property
- Life Sciences
- Materials
- Tech Scout
- Unparalleled Data Quality
- Higher Quality Content
- 60% Fewer Hallucinations
Browse by: Latest US Patents, China's latest patents, Technical Efficacy Thesaurus, Application Domain, Technology Topic, Popular Technical Reports.
© 2025 PatSnap. All rights reserved.Legal|Privacy policy|Modern Slavery Act Transparency Statement|Sitemap|About US| Contact US: help@patsnap.com