Manufacturing method of strip-shaped stator core lamination and mold arrangement therefor
A belt-shaped stator, a technology for a manufacturing method, applied in a manufacturing method and a mold device for the same, and a mold device field, and can solve the problems of embedding and difficulty in separating the belt-shaped core pieces 95 from each other.
- Summary
- Abstract
- Description
- Claims
- Application Information
AI Technical Summary
Problems solved by technology
Method used
Image
Examples
Embodiment Construction
[0059] Next, referring to the attached drawings, the embodiment of the present invention will be described for understanding of the present invention.
[0060] Such as figure 1 As shown, the method for manufacturing a strip-shaped stator core sheet according to an embodiment of the present invention includes first and second strip-shaped stator core sheets (hereinafter also simply referred to as strip-shaped core sheets) 10 and 11, and the strip-shaped The magnetic pole piece parts 12 and 13 of the core pieces 10 and 11 are discharged on the magnetic strip 14 in the meshed state, and the strip-shaped core pieces 10 and 11 are separated from the magnetic strip 14 by press working. Forming process, slit punching process, shearing process, straightening process and separation process. Next, it will be described in detail.
[0061] (preparation process)
[0062] The first and second strip-shaped core pieces 10 and 11 are laid out on a magnetic strip 14 made of an electromagnet...
PUM
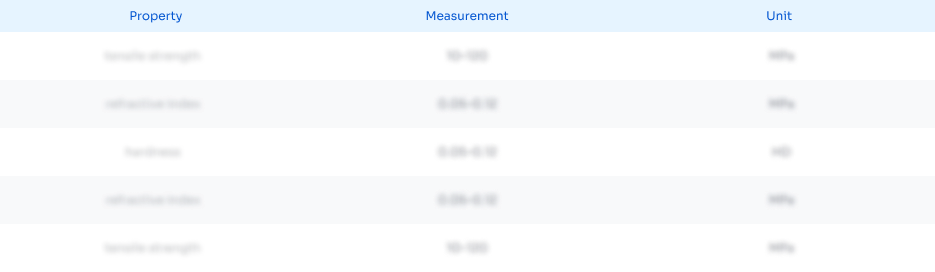
Abstract
Description
Claims
Application Information

- R&D
- Intellectual Property
- Life Sciences
- Materials
- Tech Scout
- Unparalleled Data Quality
- Higher Quality Content
- 60% Fewer Hallucinations
Browse by: Latest US Patents, China's latest patents, Technical Efficacy Thesaurus, Application Domain, Technology Topic, Popular Technical Reports.
© 2025 PatSnap. All rights reserved.Legal|Privacy policy|Modern Slavery Act Transparency Statement|Sitemap|About US| Contact US: help@patsnap.com