Method for measuring minimum wall thickness between holes
An inspection method, the smallest technology, applied in the direction of mechanical thickness measurement, measuring devices, instruments, etc., can solve the problems of complex inspection process, scrapped sample parts, and inability to guarantee parts qualified, etc., to simplify the inspection process, easy to operate, and reduce misjudgment The effect of the probability of
- Summary
- Abstract
- Description
- Claims
- Application Information
AI Technical Summary
Problems solved by technology
Method used
Image
Examples
Embodiment Construction
[0018] The specific embodiments of the present invention will be described in detail below in conjunction with the accompanying drawings, but it should be understood that the protection scope of the present invention is not limited by the specific embodiments.
[0019] Unless expressly stated otherwise, throughout the specification and claims, the term "comprise" or variations thereof such as "includes" or "includes" and the like will be understood to include the stated elements or constituents, and not Other elements or other components are not excluded.
[0020] The processing conditions of the two disjoint inner holes according to the specific embodiment of the present invention are as described in the background technology: two inner cylindrical holes 1, 2 with radii a and b are processed by two drill bits on the same machine tool, Their positions are relatively fixed. And the inner cylindrical hole 3 whose diameter is c is drilled from another plane by a drill bit of ano...
PUM
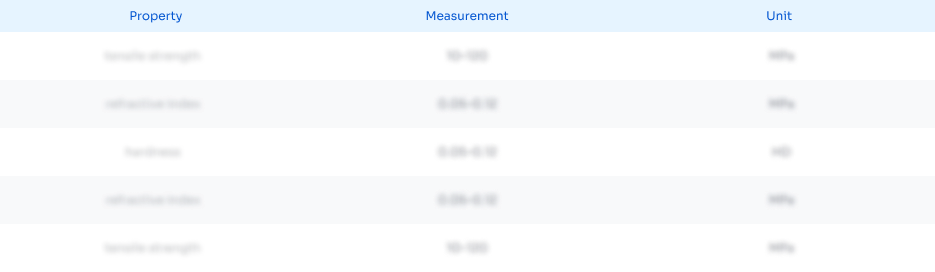
Abstract
Description
Claims
Application Information

- R&D Engineer
- R&D Manager
- IP Professional
- Industry Leading Data Capabilities
- Powerful AI technology
- Patent DNA Extraction
Browse by: Latest US Patents, China's latest patents, Technical Efficacy Thesaurus, Application Domain, Technology Topic, Popular Technical Reports.
© 2024 PatSnap. All rights reserved.Legal|Privacy policy|Modern Slavery Act Transparency Statement|Sitemap|About US| Contact US: help@patsnap.com