High performance soft magnetic composite Ni-Zn ferrite material
A ferrite material and soft magnetic composite technology, applied in the field of soft magnetic ferrite, can solve the problems of product bursting, affecting reliability, damage and so on
- Summary
- Abstract
- Description
- Claims
- Application Information
AI Technical Summary
Problems solved by technology
Method used
Image
Examples
preparation example Construction
[0039] The preparation method of above-mentioned formula is:
[0040] 1) Mixing for one-time sanding: mix ingredients according to the main formula and add 1.0 wt % PVA for wet sanding, where the mass ratio of (material: ball: water) is (1:8:0.6), and the sanding time is 1.0Hr ~1.5 Hr;
[0041] 2) Spray drying: Dry and granulate the sanded slurry with a pressure sprayer to make spherical granules. The drying temperature is controlled at 300°C~360°C and the pressure is controlled at 2.0~2.4MPa;
[0042] 3) Pre-burning: Send the sprayed pellets to the rotary kiln for pre-burning, the pre-burning temperature is controlled at 900°C±20°C, and the pre-burning time is 2.0Hr~3.5Hr;
[0043] 4) Secondary sanding: Add the specified amount of trace additives, pre-fired main component materials, and 2.0 wt % PVA into the sand mill for sanding, and the ratio of (material: ball: water) is ( 1:8:0.6), sanding time is 2.0Hr~3.0Hr;
[0044] 5) Centrifugal granulation: Dry the sanded slurry ...
Embodiment
[0061] The DC bias data of the embodiment is as follows: (unit: uH)
[0062]
[0063] The comparison ratio DC bias data is as follows: (unit: uH)
[0064]
[0065] Note: The source of the comparative example is the same model product of a famous domestic company, and the magnetic characteristics are: Bs=410mT, ui=360;
[0066] from figure 1 It can be seen that the bias curve characteristic of the embodiment of the present invention is obviously better than that of the comparative example. When maintaining the same inductance value of 80%, the embodiment is 1.23A while the comparative example is only 0.94A, which is 30% higher than that of the embodiment.
[0067] By adding TiO 2 、 Bi 2 o 3 Substances that can make the crystallization and refinement of the material uniform in pores (see attached figure 2 ); and because the stress generated by the instantaneous thermal shock will be transmitted through the grains and gradually decrease, so the refined grains can damp...
PUM
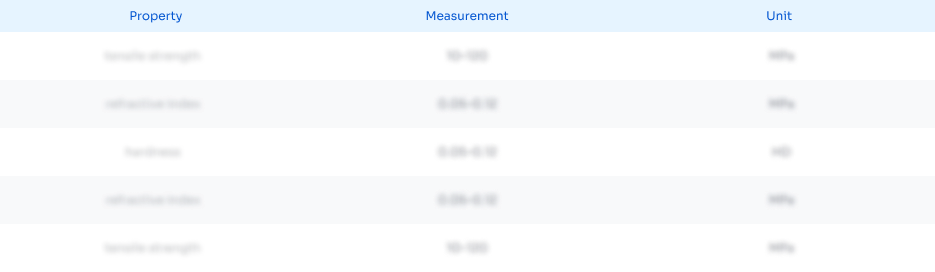
Abstract
Description
Claims
Application Information

- R&D Engineer
- R&D Manager
- IP Professional
- Industry Leading Data Capabilities
- Powerful AI technology
- Patent DNA Extraction
Browse by: Latest US Patents, China's latest patents, Technical Efficacy Thesaurus, Application Domain, Technology Topic, Popular Technical Reports.
© 2024 PatSnap. All rights reserved.Legal|Privacy policy|Modern Slavery Act Transparency Statement|Sitemap|About US| Contact US: help@patsnap.com