Roller synchronous feeding device
A technology of feeding device and material guiding device, applied in the direction of feeding device, positioning device, storage device, etc., can solve the problems of small force, sheet bending, and large force, etc.
- Summary
- Abstract
- Description
- Claims
- Application Information
AI Technical Summary
Problems solved by technology
Method used
Image
Examples
Embodiment 1
[0013] like figure 1 As shown, a shaft-roller synchronous feeding device includes a frame 1, a casing 6, a driving roller 2 and a driven roller 3, the casing 6 is installed on the frame 1 through bolts, and the casing 6 is provided with a feeding port And the discharge port, the driving roller 2 is driven by a motor, and the driving roller 2 is located under the driven roller 3. In this embodiment, the motor is a commonly used ordinary motor. 6 connections such as figure 2 As shown, an adjustment mechanism is also provided. The adjustment mechanism includes an adjustment rod 5, an adjustment nut 7 and an adjustment seat 10. Both sides of the driven roller 3 are provided with an adjustment mechanism. The adjustment seat 10 is connected, the adjustment rod 5 is fixedly connected with the adjustment seat 10, and the adjustment rod 5 vertically penetrates the upper part of the housing 6, the adjustment nut 7 is threaded with the upper end of the adjustment rod 5, and the adjustm...
Embodiment 2
[0017] Different from Embodiment 1, the material guide device is a guide wheel located on both sides of the plate 8, and the guide plane formed by the guide wheels on both sides is equal to the upper surface of the driving roller 2, and the guide wheels on both sides can limit the vertical direction of the plate 8. The deviation in the direction and horizontal direction, and the plate 8 can enter between the driving roller 2 and the driven roller 3 straightly.
[0018] Specific workflow:
[0019] like figure 1 As shown, first adjust the adjustment mechanism on both sides of the driven roller 3 according to the thickness of the plate 8, and then adjust the adjustment nut 7, the driven roller 3 can move vertically, and adjust to the alignment between the driving roller 2 and the driven roller 3. 8 After extrusion, start the motor, and the motor drives the driving roller 2 to rotate, such as figure 2 As shown, since the driving roller 2 and the driven roller 3 are respectively...
PUM
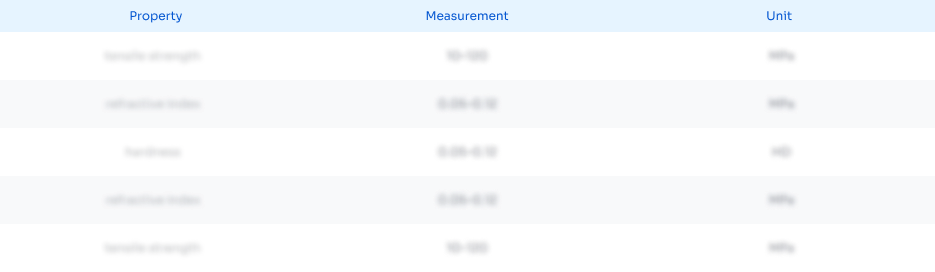
Abstract
Description
Claims
Application Information

- R&D
- Intellectual Property
- Life Sciences
- Materials
- Tech Scout
- Unparalleled Data Quality
- Higher Quality Content
- 60% Fewer Hallucinations
Browse by: Latest US Patents, China's latest patents, Technical Efficacy Thesaurus, Application Domain, Technology Topic, Popular Technical Reports.
© 2025 PatSnap. All rights reserved.Legal|Privacy policy|Modern Slavery Act Transparency Statement|Sitemap|About US| Contact US: help@patsnap.com