Simulation design method for rolling hole patterns of steel rail
A technology of simulation design and pass design, applied in computing, special data processing applications, instruments, etc., can solve the problems of roll processing errors, high labor intensity, scrap rolls, etc., to avoid errors, reduce labor intensity, and improve accuracy. Effect
- Summary
- Abstract
- Description
- Claims
- Application Information
AI Technical Summary
Problems solved by technology
Method used
Image
Examples
Embodiment 1
[0026] On the basis of the secondary development module of AutoCAD, the whole process of realizing the background sub-network operation without manual operation by using the bottom layer to call ANSYS pre-processing is as follows,
[0027] (1) First, according to the position of each key point calculated by the secondary development module of AutoCAD, a file recognizable by ANSYS is generated, and its implementation code is:
[0028] Dim uproller As Variant
[0029] Open uproller For Output As1#
[0030] Print#1," / PREP7"
[0031] Print#1," / NERR,0,99999,,,0"
[0032] Print#1,"EDMP,RIGI,1,0,0"
[0033] Print#1,"MP,DENS,1,7"
[0034] Print#1,"K,";pt1(0);",";pt1(1);",";pt1(2)
[0035] Print#1,"K,";pt2(0);",";pt2(1);",";pt2(2)
[0036] ...
[0037] Print#1,"LSTR,3,4"
[0038] Print#1,"LFILLT,1,2,"; convert(HR2); ",,"
[0039] Print#1,"LFILLT,2,3,"; convert(HR1); ",,"
[0040] Print#1,"K,";pt1(0);",";pt1(1)+d;",";pt1(2)
[0041] ...
[0042] Print#1,"LESIZE,3,";kxcc;",,,...
Embodiment 2
[0074] Taking a certain H-shaped steel BD1 roll matching as an example, the whole process of realizing the CAM module is introduced.
[0075] (1) First, according to the secondary development module of AutoCAD, calculate the position of each key point of the BD1 roll, and generate the CAD graphics of the BD1 roll.
[0076] (2) According to the position of each key point of the BD1 roll, combined with the format of the on-site CNC machining machine tool system, a machining code that can be recognized by machining is generated, and its realization code is:
[0077] Open text For Output As1#
[0078] Print#1,"1.DIAMOF"
[0079] Print#1,"2.M3S"; zs
[0080] Print#1,"3.G54T";num1;"D";num2
[0081] Print#1,"4.G0G90G95G41X560Z-50F"; sd
[0082] Print#1,"5.G1X"; CStr(ncL5 / 2-ncR1-10)
[0083] Print#1,"6.Z0"
[0084] Print#1,"7.G91X"; CStr(ncR1+10); "RND="; CStr(ncR1)
[0085] Print#1,"8.Z"; CStr(L)
[0086] Print#1,"9.X"; CStr((ncL1-ncL2) / 2)
[0087] Print#1,"10.Z"; CStr(ncL9+...
PUM
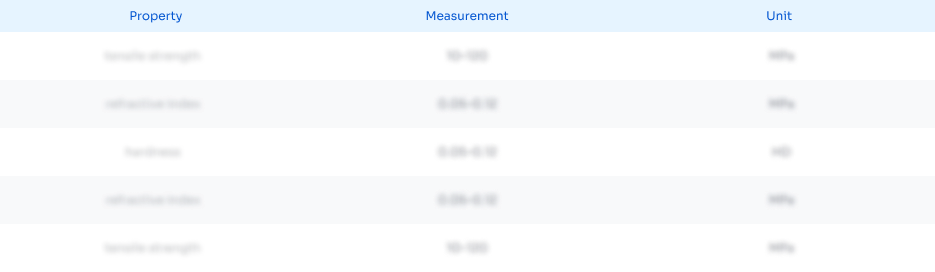
Abstract
Description
Claims
Application Information

- R&D
- Intellectual Property
- Life Sciences
- Materials
- Tech Scout
- Unparalleled Data Quality
- Higher Quality Content
- 60% Fewer Hallucinations
Browse by: Latest US Patents, China's latest patents, Technical Efficacy Thesaurus, Application Domain, Technology Topic, Popular Technical Reports.
© 2025 PatSnap. All rights reserved.Legal|Privacy policy|Modern Slavery Act Transparency Statement|Sitemap|About US| Contact US: help@patsnap.com