Oil bottle drying device
A drying device and oil bottle technology, applied in drying, drying machine, drying gas arrangement, etc., can solve the problems of manual bottle changing, low drying efficiency, time-consuming and laborious, etc., to ensure continuous operation, good drying, and prevent skewed effect
- Summary
- Abstract
- Description
- Claims
- Application Information
AI Technical Summary
Problems solved by technology
Method used
Image
Examples
Embodiment Construction
[0012] The present invention will be further described below in conjunction with the accompanying drawings and embodiments.
[0013] Such as figure 1 As shown, an oil bottle drying device includes a drying box 1 and a conveyor belt 2, the conveyor belt 2 passes through the drying box 1, and the drying box 1 is divided into a warm air area 11 and a cold air area 12. An air outlet 13 is provided on the drying box wall of the warm air area 11 and the cold area 12, and the conveyor belt 2 passes through the warm air area 11 and the cold air area 12 in sequence; the conveyor belt Railings 3 are provided on the left and right sides of the conveyor belt 3, and the railings 3 include a baffle 31 and a pressing plate 32. The baffle 31 is arranged on both sides of the conveyor belt 2, and the pressing plate 32 is vertically connected with the baffle 31. At least two air outlets 13 are provided on the dryer box wall of the warm air area 11 and the cold subregion 12; All are provided wi...
PUM
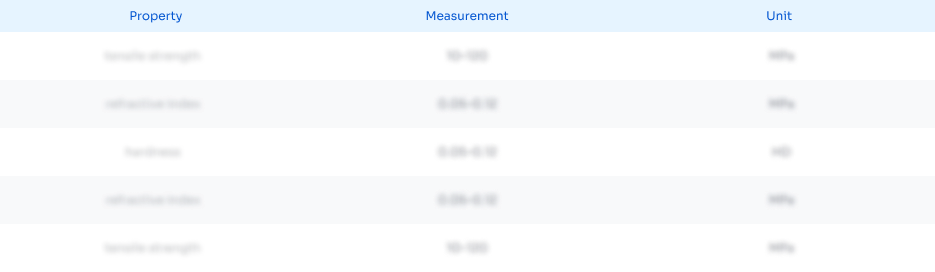
Abstract
Description
Claims
Application Information

- R&D Engineer
- R&D Manager
- IP Professional
- Industry Leading Data Capabilities
- Powerful AI technology
- Patent DNA Extraction
Browse by: Latest US Patents, China's latest patents, Technical Efficacy Thesaurus, Application Domain, Technology Topic, Popular Technical Reports.
© 2024 PatSnap. All rights reserved.Legal|Privacy policy|Modern Slavery Act Transparency Statement|Sitemap|About US| Contact US: help@patsnap.com