Coating machine for panels or coiled materials
A coating machine and coating technology, which is applied to the device and coating of the surface coating liquid, can solve the problems of reduced production efficiency, unreasonable structure, and increased cost, and achieve the effect of improving production efficiency and avoiding waste
- Summary
- Abstract
- Description
- Claims
- Application Information
AI Technical Summary
Problems solved by technology
Method used
Image
Examples
Embodiment Construction
[0022] The present invention will be described in further detail below through specific examples.
[0023] Such as figure 1 , 2 As shown, a coating machine for plates or coils includes a frame 1 and a number of conveying rollers fixed on the frame 1. The conveying rollers are arranged according to the conveying length of the plates or coils and the routing of the entire space. In this example, if figure 1 As shown, the conveying rollers include two pure conveying rollers 2 rotating on the frame 1 and two backing rollers 3 , and the backing rollers 3 are symmetrically arranged left and right with respect to the vertical center line of the frame 1 . The plate or coil enters the coating machine after the previous process, and enters the drying box after passing through the pure conveying roller 2, two backing rollers 3 and another pure conveying roller 2. The backing roller 3 not only acts To the conveying function, but also cooperate with the painting mechanism to paint the p...
PUM
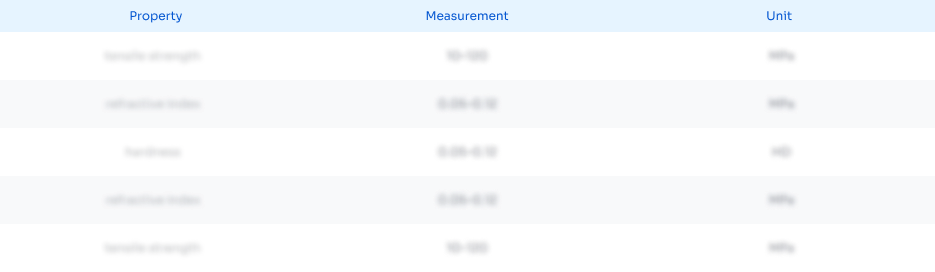
Abstract
Description
Claims
Application Information

- R&D
- Intellectual Property
- Life Sciences
- Materials
- Tech Scout
- Unparalleled Data Quality
- Higher Quality Content
- 60% Fewer Hallucinations
Browse by: Latest US Patents, China's latest patents, Technical Efficacy Thesaurus, Application Domain, Technology Topic, Popular Technical Reports.
© 2025 PatSnap. All rights reserved.Legal|Privacy policy|Modern Slavery Act Transparency Statement|Sitemap|About US| Contact US: help@patsnap.com