A kind of chloroprene rubber mixing process
A chloroprene rubber mixing technology, applied in the field of chloroprene rubber mixing technology, can solve the problems of rough surface of extruded products, poor mixing effect of internal mixer temperature rise, etc., and achieve stable performance of finished products
- Summary
- Abstract
- Description
- Claims
- Application Information
AI Technical Summary
Problems solved by technology
Method used
Image
Examples
Embodiment 1
[0033] Neoprene was made using the technology of the present application.
[0034] a. Thin pass plastication of neoprene: Put 50kg of neoprene into the open mill, roll and weigh it after 5 passes to form a plasticized film, and park it overnight, in which the distance between the two rollers of the open mill is controlled is 1mm, and the roller temperature is controlled at 30°C;
[0035] b. One-stage internal mixing: After heating the internal mixer to 40°C, put the plasticized film that was parked overnight in step a into the internal mixer, and at the same time put 3kg of anti-scorch agent into the internal mixer, press down the top bolt and mix for 1min, then raise the upper Put 50kg of reinforcing filler into the top bolt, observe the change of mixing temperature and power, when the temperature rises to 75°C, raise the top bolt and put in 6kg of softener to continue mixing;
[0036] c. One-stage degumming: When the power curve tends to be stable and the temperature rea...
Embodiment 2
[0039] The specific production steps are:
[0040] a. One-stage internal mixing: After heating the internal mixer to 40°C, put 50kg of neoprene into the internal mixer, and at the same time, put in 3kg of anti-scorch agent, press down the upper top bolt and mix for 1min, then raise the upper top bolt and put in 50kg of supplementary For strong fillers, when the temperature rises to 75°C, raise the top bolt and put in 6kg of softener to continue mixing until the temperature reaches 100°C for debinding, and park overnight;
[0041] b. Second-stage internal mixing: Put the mixed rubber parked overnight in step a into the internal mixer again, and at the same time put in the vulcanizing agent, and directly discharge the rubber after mixing for 60 seconds to obtain a semi-finished product.
Embodiment 3
[0043] The specific production steps are:
[0044] a. Neoprene rubber mastication: put 50kg neoprene rubber into the open mill, roll and weigh it after 5 passes to form a masticated rubber roll, and park it overnight. The roller temperature is controlled at 30°C;
[0045] b. One-stage internal mixing: After heating the internal mixer to 40°C, put the plasticized film that was parked overnight in step a into the internal mixer, and at the same time put 3kg of anti-scorch agent into the internal mixer, press down the top bolt and mix for 1min, then raise the upper Add 50kg of reinforcing filler and 6kg of softener to the top bolt and continue mixing;
[0046] c. One-stage degumming: degumming when the temperature reaches 100°C, and park overnight;
[0047] d. Second-stage internal mixing: Put the mixed rubber parked overnight in step d into the internal mixer again, and at the same time put in the vulcanizing agent, and directly discharge the rubber after mixing for 60 seco...
PUM
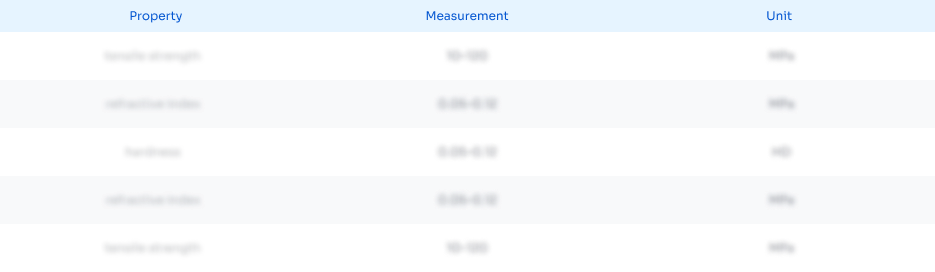
Abstract
Description
Claims
Application Information

- R&D
- Intellectual Property
- Life Sciences
- Materials
- Tech Scout
- Unparalleled Data Quality
- Higher Quality Content
- 60% Fewer Hallucinations
Browse by: Latest US Patents, China's latest patents, Technical Efficacy Thesaurus, Application Domain, Technology Topic, Popular Technical Reports.
© 2025 PatSnap. All rights reserved.Legal|Privacy policy|Modern Slavery Act Transparency Statement|Sitemap|About US| Contact US: help@patsnap.com