Ship component molding bed manufacturing process
A production process and tire frame technology, which is applied to ship parts, ship construction, ships, etc., can solve the problems of difficult assembly, inconvenient disassembly and assembly, and achieve the effects of saving time, convenient disassembly, and simple operation.
- Summary
- Abstract
- Description
- Claims
- Application Information
AI Technical Summary
Problems solved by technology
Method used
Examples
Embodiment 1
[0021] An assembly process for ship parts, comprising the steps of:
[0022] (1) The selection of frame datum is mainly determined according to the change of hull or molded line and the improvement of construction conditions. The minimum height of the entire tire frame is generally 1.30 meters, and the minimum height shall not be less than 1.20 meters;
[0023] (2) Tangential tire frame: when the base plane of the tire frame is parallel to the base line of the ship bottom and perpendicular to the plane of the frame, it is suitable for the bottom section, deck section and side section with less linear change. The cut tire frame is relatively easy to manufacture, segmented, welded, and marked;
[0024] (3) Single bevel cut tire frame: when the side section with a small rib series in the rib line type can adopt single bevel cut (also known as positive bevel cut;
[0025] (4) Chamfered frame: For the side sections with large bow and stern curvature changes, double chamfered fram...
Embodiment 2
[0033] An assembly process for ship parts, comprising the steps of:
[0034] (1) The selection of frame datum is mainly determined according to the change of hull or molded line and the improvement of construction conditions. The minimum height of the entire tire frame is generally 1.30 meters, and the minimum height shall not be less than 1.20 meters;
[0035] (2) Tangential tire frame: when the base plane of the tire frame is parallel to the base line of the ship bottom and perpendicular to the plane of the frame, it is suitable for the bottom section, deck section and side section with less linear change. The cut tire frame is relatively easy to manufacture, segmented, welded, and marked;
[0036] (3) Single bevel cut tire frame: when the side section with a small rib series in the rib line type can adopt single bevel cut (also known as positive bevel cut;
[0037] (4) Chamfered frame: For the side sections with large bow and stern curvature changes, double chamfered fram...
Embodiment 3
[0045] An assembly process for ship parts, comprising the steps of:
[0046](1) The selection of frame datum is mainly determined according to the change of hull or molded line and the improvement of construction conditions. The minimum height of the entire tire frame is generally 1.30 meters, and the minimum height shall not be less than 1.20 meters;
[0047] (2) Tangential tire frame: when the base plane of the tire frame is parallel to the base line of the ship bottom and perpendicular to the plane of the frame, it is suitable for the bottom section, deck section and side section with less linear change. The cut tire frame is relatively easy to manufacture, segmented, welded, and marked;
[0048] (3) Single bevel cut tire frame: when the side section with a small rib series in the rib line type can adopt single bevel cut (also known as positive bevel cut;
[0049] (4) Chamfered frame: For the side sections with large bow and stern curvature changes, double chamfered frame...
PUM
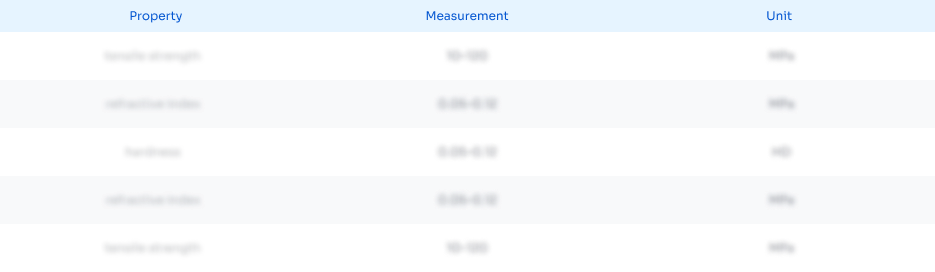
Abstract
Description
Claims
Application Information

- R&D
- Intellectual Property
- Life Sciences
- Materials
- Tech Scout
- Unparalleled Data Quality
- Higher Quality Content
- 60% Fewer Hallucinations
Browse by: Latest US Patents, China's latest patents, Technical Efficacy Thesaurus, Application Domain, Technology Topic, Popular Technical Reports.
© 2025 PatSnap. All rights reserved.Legal|Privacy policy|Modern Slavery Act Transparency Statement|Sitemap|About US| Contact US: help@patsnap.com