Grinding wheel for high-speed railway
A high-speed railway and grinding wheel technology, applied in the direction of bonded grinding wheels, abrasives, metal processing equipment, etc., can solve the problems of harsh grinding conditions, large grinding load, large contact surface, etc. The effect of increased adhesion
- Summary
- Abstract
- Description
- Claims
- Application Information
AI Technical Summary
Problems solved by technology
Method used
Image
Examples
Embodiment Construction
[0011] As shown in the figure, a grinding wheel for high-speed railways includes a grinding wheel base 1 and a grinding wheel main body 2, the grinding wheel main body 2 is fixed above the grinding wheel base 1, and the grinding wheel base 1 includes a base 3 on which the A first baffle plate 4, a second baffle plate 5, a third baffle plate 6 and a fourth baffle plate 7 are provided in the circumferential direction in turn from the inside to the outside. The height of the first baffle plate 4 is H1, and the height of the second baffle plate 5 is H2, the height of the third baffle plate 6 is H3, the height of the fourth baffle plate 7 is H4, the radius of the first baffle plate 4 is r1, the radius of the second baffle plate 5 is r2, and the radius of the third baffle plate 6 is r2. The radius is r3, the radius of the fourth baffle plate 7 is r4, H1=H4<H2<H3, r4-r3=r3-r2=r2-r1, the outer circumference of the first baffle plate 4 is provided with a ring of raised lines 8, so The ...
PUM
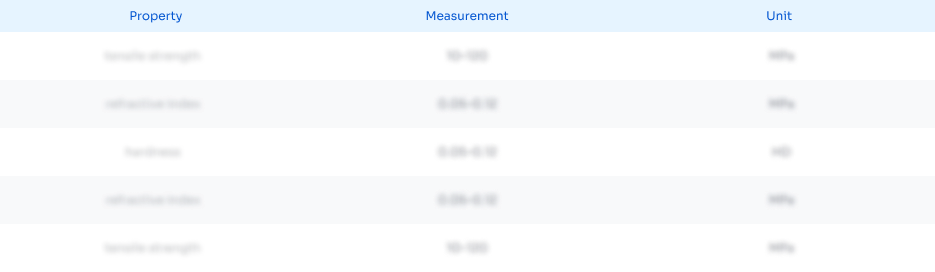
Abstract
Description
Claims
Application Information

- Generate Ideas
- Intellectual Property
- Life Sciences
- Materials
- Tech Scout
- Unparalleled Data Quality
- Higher Quality Content
- 60% Fewer Hallucinations
Browse by: Latest US Patents, China's latest patents, Technical Efficacy Thesaurus, Application Domain, Technology Topic, Popular Technical Reports.
© 2025 PatSnap. All rights reserved.Legal|Privacy policy|Modern Slavery Act Transparency Statement|Sitemap|About US| Contact US: help@patsnap.com