Full-automatic filter threaded cover plate blanker
A threaded cover and fully automatic technology, applied in metal processing equipment, feeding devices, manufacturing tools, etc., can solve problems such as low production efficiency, poor safety performance, and high labor intensity, so as to reduce labor intensity and ensure life safety , to achieve the effect of automated production
- Summary
- Abstract
- Description
- Claims
- Application Information
AI Technical Summary
Problems solved by technology
Method used
Image
Examples
Embodiment 1
[0021] Embodiment 1: as figure 1 As shown, a fully automatic blanking machine for filter threaded cover provided by the present invention includes a press 1, and the press 1 is a prior art, preferably an open tilting machine produced by Jiangsu Yangli Group Co., Ltd. Press machine, described press machine 1 comprises frame 1a, and the front side of described frame 1a is provided with workbench 1b and fork 9 corresponding to each other, and the lower end of described fork 9 is connected upper mold 10, is characterized in that:
[0022] a, an automatic feeder 2 is correspondingly arranged on the front side of the press 1, the automatic feeder 2 is prior art, the automatic feeder 2 includes a body, and two symmetrical transverse slide rails 29 are passed on the body Slidingly fit to connect the feed table 24, and connect a horizontal motor 25 on the body, the horizontal motor 25 is connected with the transmission table 24 by the horizontal screw mandrel 26 and the horizontal scre...
Embodiment 2
[0027] Example 2: Combining Figure 4 As shown, the two symmetrical side walls of the frame 1a are symmetrically connected with two connecting plates 21, a reinforcing rod 22 is arranged between the two, and the two ends of the intermediate fixed shaft 20 are fixedly connected to the two On the connecting plate 21 corresponding to the side, two limiting plates 23 are also sleeved on the intermediate fixed shaft 20, and each of the limiting plates 23 is locked and fixed on the intermediate fixed shaft 20 by locking screws. , and the two limiting plates 23 are respectively arranged on both sides of the rotating sleeve 15 for limiting cooperation therewith.
[0028] Receiving principle: the cold-rolled sheet 30 of 2000mm×1250mm×3mm is held on the feeding platform 24 by the pneumatic clamp 28, the cold-rolled sheet 30 is transported to the designated position by the longitudinal motor 27, and the cold-rolled sheet 30 is transported by the transverse motor 25 Advance step by step,...
PUM
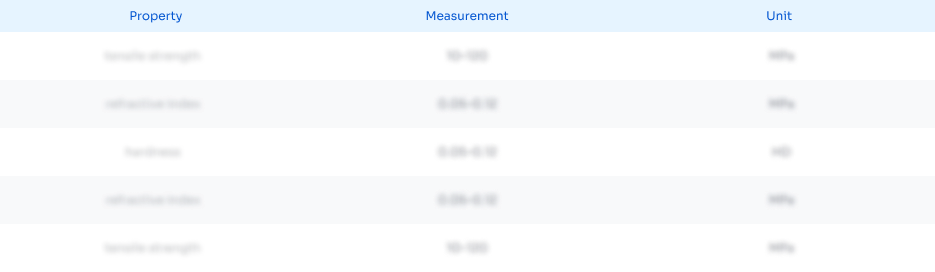
Abstract
Description
Claims
Application Information

- R&D
- Intellectual Property
- Life Sciences
- Materials
- Tech Scout
- Unparalleled Data Quality
- Higher Quality Content
- 60% Fewer Hallucinations
Browse by: Latest US Patents, China's latest patents, Technical Efficacy Thesaurus, Application Domain, Technology Topic, Popular Technical Reports.
© 2025 PatSnap. All rights reserved.Legal|Privacy policy|Modern Slavery Act Transparency Statement|Sitemap|About US| Contact US: help@patsnap.com