A heat treatment process for producing high-quality mold steel in a trolley furnace
A trolley furnace and mold steel technology, applied in heat treatment furnaces, heat treatment equipment, furnaces, etc., can solve the problems of poor temperature control accuracy, low production efficiency, long holding time, etc., to ensure uniform hardness and uniform furnace temperature performance, and the effect of preventing deformation of the steel plate
- Summary
- Abstract
- Description
- Claims
- Application Information
AI Technical Summary
Problems solved by technology
Method used
Image
Examples
Embodiment 1
[0022] The process steps of a heat treatment process for producing high-quality mold steel in a trolley furnace provided in this embodiment:
[0023] (1) Steel loading: such as figure 1 Shown: the die steel plates 3 are stacked in order from thick to thin and from bottom to top into the bogie furnace, and the upper and lower plates are supported by the section steel 2. When the furnace is installed, the three sides of the steel plate are aligned on one side, 100mm away from the furnace wall, and the other side is filled with a thin plate in the width direction, 100mm away from the furnace wall. Each layer of steel plate 3 is placed 500mm away from the head and tail of the section steel 2 for support to prevent the two ends of the steel plate 3 from being affected by high temperature after tempering. The upper and lower section steel 2 spacers at the corresponding positions of the upper and lower steel plate layers are on the same vertical line to prevent the steel plate from bend...
Embodiment 2
[0032] The process steps of a heat treatment process for producing high-quality mold steel in a trolley furnace provided in this embodiment:
[0033] (1) Steel loading: such as figure 1 Shown: the die steel plates 3 are stacked in order from thick to thin and from bottom to top into the bogie furnace, and the upper and lower plates are supported by the section steel 2. When the furnace is installed, the three sides of the steel plate are aligned on one side, 120mm away from the furnace wall, and the other side is filled with a thin plate in the width direction, 120mm away from the furnace wall. Each layer of steel plate 3 is placed 500mm away from the head and tail of the section steel 2 for support to prevent the two ends of the steel plate 3 from being affected by high temperature after tempering. The upper and lower section steel 2 spacers at the corresponding positions of the upper and lower steel plate layers are on the same vertical line to prevent the steel plate from bend...
Embodiment 3
[0042] The process steps of a heat treatment process for producing high-quality mold steel in a trolley furnace provided in this embodiment:
[0043] (1) Steel loading: such as figure 1 Shown: the die steel plates 3 are stacked in order from thick to thin and from bottom to top into the bogie furnace, and the upper and lower plates are supported by the section steel 2. When the furnace is installed, the three sides of the steel plate are aligned on one side, 150mm away from the furnace wall, and the other side is made up with a thin plate in the width direction, 150mm away from the furnace wall. Each layer of steel plate 3 is placed 500mm away from the head and tail of the section steel 2 for support to prevent the two ends of the steel plate 3 from being affected by high temperature after tempering. The upper and lower section steel 2 spacers at the corresponding positions of the upper and lower steel plate layers are on the same vertical line to prevent the steel plate from ben...
PUM
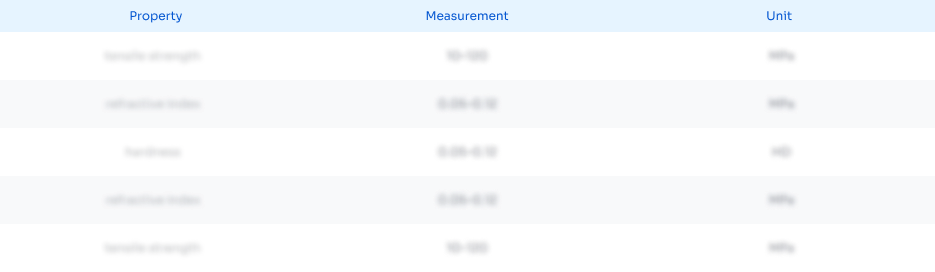
Abstract
Description
Claims
Application Information

- R&D Engineer
- R&D Manager
- IP Professional
- Industry Leading Data Capabilities
- Powerful AI technology
- Patent DNA Extraction
Browse by: Latest US Patents, China's latest patents, Technical Efficacy Thesaurus, Application Domain, Technology Topic, Popular Technical Reports.
© 2024 PatSnap. All rights reserved.Legal|Privacy policy|Modern Slavery Act Transparency Statement|Sitemap|About US| Contact US: help@patsnap.com