Method for chamfering slabs during rolling of rolling mill
A slab and chamfering technology, which is applied in the production field of fire-cut chamfering of thick slab slabs, can solve the problems of long time consumption, affecting efficiency, long chamfering time, etc., and achieve the effect of eliminating high cost.
- Summary
- Abstract
- Description
- Claims
- Application Information
AI Technical Summary
Problems solved by technology
Method used
Image
Examples
Embodiment 1
[0109] Slab size: thickness 290mm, width 2300mm, length 2700mm.
[0110] Target size of rolled steel plate: thickness 20.15mm, width 3800mm, length 11740mm.
[0111] The widening pass is calculated as 5 passes, and the first two passes meet the chamfering conditions;
[0112] The thickness of the slab before widening is 265mm; the rolling length is 3800mm of the slab width.
[0113] Settings for the first pass of widening:
[0114] The reduction is 30mm, the thickness after reduction is 235mm, the rolling length Len=4285mm after rolling, and the calculated temperature is 1121°C.
[0115] Head and tail segment length Lp=40mm,
[0116] L1=L19=30mm;
[0117] L2=L3=...L18=(4285-2*40) / 17=247mm.
[0118] The chamfering depth is set to h=20mm,
[0119] Roll gap value So=236mm before treatment,
[0120] S1p=S20p=So-h=216mm,
[0121] S2=S3=...=S19=236mm.
[0122] The setting of the second pass of widening:
[0123] The reduction is 30mm, the thickness after reduction is 205mm...
PUM
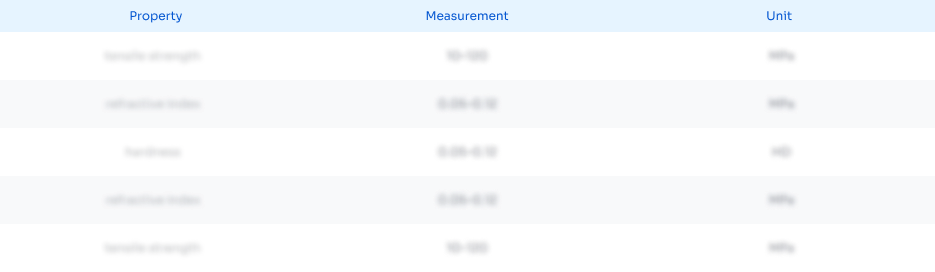
Abstract
Description
Claims
Application Information

- R&D
- Intellectual Property
- Life Sciences
- Materials
- Tech Scout
- Unparalleled Data Quality
- Higher Quality Content
- 60% Fewer Hallucinations
Browse by: Latest US Patents, China's latest patents, Technical Efficacy Thesaurus, Application Domain, Technology Topic, Popular Technical Reports.
© 2025 PatSnap. All rights reserved.Legal|Privacy policy|Modern Slavery Act Transparency Statement|Sitemap|About US| Contact US: help@patsnap.com