Optimized design method of airplane process equipment
A technology of process equipment and optimized design, applied in the direction of calculation, special data processing applications, instruments, etc., can solve the problems of inappropriate judgment of CNC machining surface and hole machining accuracy requirements, waste of processing costs, and difficult judgment, so as to reduce unnecessary The effects of testing work, shortening the processing cycle, and optimizing the frame design scheme
- Summary
- Abstract
- Description
- Claims
- Application Information
AI Technical Summary
Problems solved by technology
Method used
Image
Examples
Embodiment Construction
[0026] The following are examples to introduce the above-mentioned optimization design methods respectively:
[0027] On the fuselage assembly frame of a certain model, the frame size is optimally designed, and the frame size is finally determined.
[0028] Figure 1 to Figure 5 It shows the strain diagram of the force analysis carried out by this optimal design method. The load of the jig is 8 tons, the safety factor is 4, and the maximum deformation allowed by the jig is δ (max) = 0.045 mm.
[0029] figure 1 It is the force analysis strain diagram of plan one (square steel pipe size is 250mm, thickness is 10mm, frame weight is 11757KG), the maximum deformation is 0.061mm, which does not meet the requirements.
[0030] figure 2 It is the force analysis strain diagram of plan 2 (the size of the square steel pipe is 300mm, the thickness is 8mm, and the frame weight is 12083KG), and the maximum deformation is 0.049mm, which does not meet the requirements.
[0031] ...
PUM
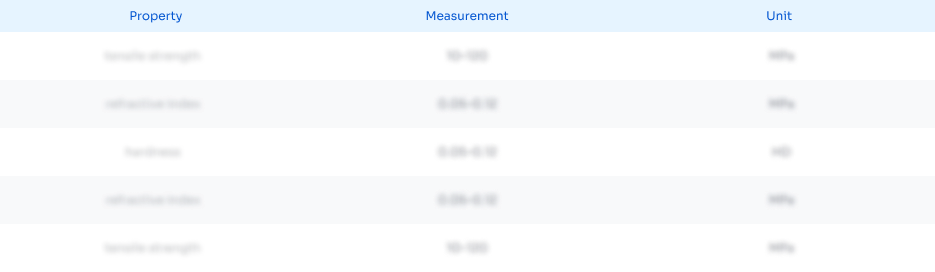
Abstract
Description
Claims
Application Information

- R&D
- Intellectual Property
- Life Sciences
- Materials
- Tech Scout
- Unparalleled Data Quality
- Higher Quality Content
- 60% Fewer Hallucinations
Browse by: Latest US Patents, China's latest patents, Technical Efficacy Thesaurus, Application Domain, Technology Topic, Popular Technical Reports.
© 2025 PatSnap. All rights reserved.Legal|Privacy policy|Modern Slavery Act Transparency Statement|Sitemap|About US| Contact US: help@patsnap.com