Method for testing faults of antiskid brake control box under complex working conditions
A technology of anti-skid brakes and complex working conditions, which is applied in the direction of electrical testing/monitoring, etc., and can solve problems such as the failure of anti-skid brake control boxes
- Summary
- Abstract
- Description
- Claims
- Application Information
AI Technical Summary
Problems solved by technology
Method used
Image
Examples
Embodiment 1
[0088] This embodiment is to conduct a comprehensive environmental stress and working current test on the anti-skid brake control box of the brake system of the first domestic branch line transport aircraft. If a failure occurs during the test, technical improvement suggestions are proposed for the failure until the test process fails. malfunction. The specific steps of this embodiment are:
[0089] Step 1. Determine the high temperature value that applies comprehensive environmental stress to the anti-skid brake control box
[0090] The high temperature value for applying environmental stress to the anti-skid brake control box is determined according to the high temperature working limit, which is lower than 5℃ of the high temperature working limit.
[0091] When determining the high temperature value of the comprehensive environmental stress test, first, according to the method of determining the high temperature working stress limit of the aircraft anti-skid brake control box dis...
Embodiment 2
[0145] The processes of Example 2 and Example 3 both include determining the high and low temperature values of the comprehensive environmental stress, determining the temperature change rate of the comprehensive environmental stress, determining the vibration set point of the comprehensive environmental stress and the vibration increment and microvibration amount of each cycle Value and micro-vibration time, determine the operating current and operating frequency applied during the test, determine the temperature holding time in the high temperature and low temperature phases of the test, determine the performance test time and test items during the test, and formulate the test profile for complex working conditions. Test profile test, test and verify the improved anti-skid brake control box and other steps. The specific process is the same as that of Example 1, the difference is that the test data in Example 2 and Example 3 are different from the test data in Example 1. See ...
PUM
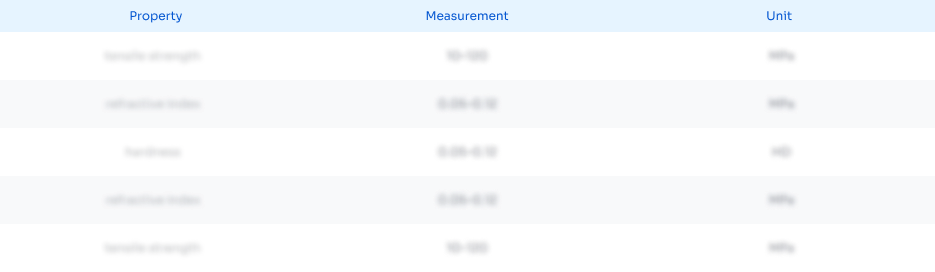
Abstract
Description
Claims
Application Information

- R&D Engineer
- R&D Manager
- IP Professional
- Industry Leading Data Capabilities
- Powerful AI technology
- Patent DNA Extraction
Browse by: Latest US Patents, China's latest patents, Technical Efficacy Thesaurus, Application Domain, Technology Topic, Popular Technical Reports.
© 2024 PatSnap. All rights reserved.Legal|Privacy policy|Modern Slavery Act Transparency Statement|Sitemap|About US| Contact US: help@patsnap.com