Converter sinter sizing process and sintering machine screening and sizing machine for converter
A sintering machine and sintering ore technology, which is applied in the direction of filter screen, solid separation, grille, etc., can solve the problems of unbalanced iron sintering supply and demand, waste, uneven composition, etc., shorten the oxidation time, increase the output of sintered ore, reduce The effect of repeated processing
- Summary
- Abstract
- Description
- Claims
- Application Information
AI Technical Summary
Problems solved by technology
Method used
Image
Examples
Embodiment Construction
[0023] A converter sinter sizing process is to select the finished sinter as cooling agent for blowing, including steps:
[0024] (1) Screening steps of finished sintered ore: screen the finished sintered ore, select the sintered ore with a particle size of 5-11 mm as the blowing coolant, and the specific screening method is: first pass through the upper sintered ore with a sieve hole of 14.5 mm The sieve 4 is screened, and the screened material is sent to the first-stage sieve A with a sieve hole of 5-7mm, and the second-stage sieve B with a sieve hole of 9-11mm for screening, and the finished sintered ore with a size of 5=11 mm is screened out;
[0025] (2) Shipping steps: such as figure 1 , 2 As shown, a first-stage conveyor belt 1 with two-way conveying function is set, and a second-stage conveyor belt 2 and a third-stage conveyor belt 3 are respectively arranged at the outlets at both ends of the first-stage conveyor belt 1. By adjusting the first The feeding direction ...
PUM
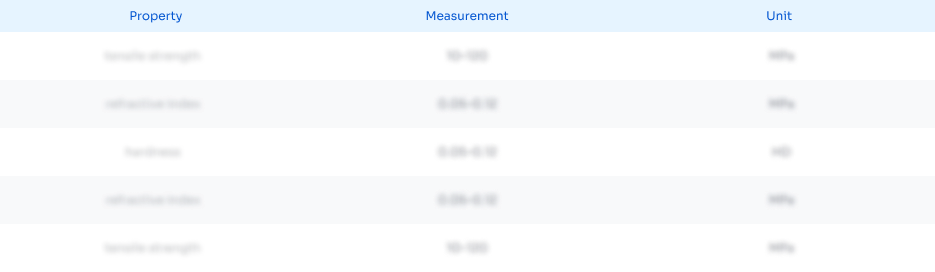
Abstract
Description
Claims
Application Information

- R&D Engineer
- R&D Manager
- IP Professional
- Industry Leading Data Capabilities
- Powerful AI technology
- Patent DNA Extraction
Browse by: Latest US Patents, China's latest patents, Technical Efficacy Thesaurus, Application Domain, Technology Topic, Popular Technical Reports.
© 2024 PatSnap. All rights reserved.Legal|Privacy policy|Modern Slavery Act Transparency Statement|Sitemap|About US| Contact US: help@patsnap.com