A high-power heat-exchanging burner for industrial furnaces
A high-power, heat-exchange technology, used in burners, gas fuel burners, combustion methods, etc., can solve the problems of short service life, inconvenient installation, poor heat exchange effect, etc. The effect of improving the use efficiency and heat exchange efficiency
- Summary
- Abstract
- Description
- Claims
- Application Information
AI Technical Summary
Problems solved by technology
Method used
Image
Examples
Embodiment
[0027] Such as figure 1 As shown, the high-power heat exchange burner described in this embodiment mainly includes a heat exchanger 1, an air inlet pipe 4 arranged on the heat exchanger 1, and a combustion chamber connected to the heat exchanger 1 and the air inlet pipe 4 3. The mixer 2 arranged inside the combustion chamber 3, the ejector 5 communicated with the air inlet pipe 4, and the main gun 6 and the ignition gun 7 communicated with the mixer 2.
[0028] Wherein, the heat exchanger 1 is the core heat exchange component of this embodiment, and its specific structure is as follows: figure 2 shown. That is to say, the heat exchanger 1 as a whole is a coaxial circular seam structure with more than 3 layers, which is mainly composed of an exchange cylinder 11, an inner finned tube 12 set on the outer side of the exchanged tube 11, and an outer finned tube 12 placed on the outer side of the inner finned tube 12. The fin tube 13 is composed of a shell 14 sleeved on the outs...
PUM
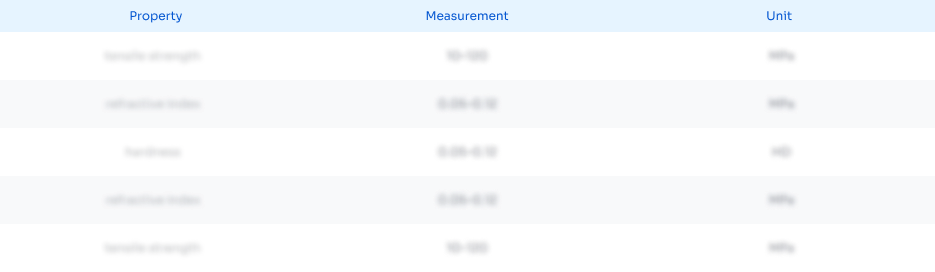
Abstract
Description
Claims
Application Information

- R&D
- Intellectual Property
- Life Sciences
- Materials
- Tech Scout
- Unparalleled Data Quality
- Higher Quality Content
- 60% Fewer Hallucinations
Browse by: Latest US Patents, China's latest patents, Technical Efficacy Thesaurus, Application Domain, Technology Topic, Popular Technical Reports.
© 2025 PatSnap. All rights reserved.Legal|Privacy policy|Modern Slavery Act Transparency Statement|Sitemap|About US| Contact US: help@patsnap.com