Glazes made from tailings resources and their glazing process
A resource and glaze technology, applied in the field of raw materials for ceramic products, can solve the problems of little change in surface color and pattern effect, unused tailings slag, environmental pollution, etc., to improve the comprehensive utilization rate of resources, maintain recyclable development, The effect of reducing production costs
- Summary
- Abstract
- Description
- Claims
- Application Information
AI Technical Summary
Problems solved by technology
Method used
Examples
Embodiment 1
[0035] 52% of feldspar, 12% of quartz, 21% of iron ore tailings, 4% of limestone, 5% of kaolin and 6% of ashes, the weight ratio of the components is: 2 parts K 2 O, 6 copies of AL 2 o 3 , 63 SiO 2 , 4 copies of P 2 o 5 , 4 Na 2 O, 7 Fe 2 o 3 , 10 parts of CaO and 6 parts of MgO, put them into the ball mill for ball milling, add water, and the ball milling time is 8 hours. After uniform mixing and stirring and fully dissolving, the glaze slurry is obtained. The remaining 0.01% is sieved; the above ball-milled glaze slurry is released from the ball mill, stored in the slurry storage tank and stirred; the glaze slurry passes through a 200-mesh sieve, and the fully suspended glaze slurry is coated on the surface of the body with a concentration of 40 Baume degrees , the thickness of the glaze on the surface of the green body is 0.7mm; when the glaze slurry is applied to the surface of the green body, the green body is wiped with water and dried, and the moisture content of...
Embodiment 2
[0037] 46% feldspar, 22% quartz, 15% iron ore tailings, 5% limestone, 3% kaolin and 9% ashes, the weight ratio of the components is: 3 parts K 2 O, 7 copies of AL 2 o 3 , 58 SiO 2 , 5 copies of P 2 o 5 , 3 Na 2 O, 4 Fe 2 o 3 , 14 parts of CaO and 4 parts of MgO, put them into the ball mill for ball milling, add water, and the ball milling time is 8.5 hours. After uniform mixing and stirring and fully dissolving, the glaze slurry is obtained, and the fineness of the glaze slurry is controlled at a million-hole sieve The remaining 0.008% is sieved; release the above ball-milled glaze slurry from the ball mill, store it in the slurry storage tank and stir; pass the glaze slurry through a 200-mesh sieve, and apply the fully suspended glaze slurry on the surface of the green body with a concentration of 39 degrees Baume , the thickness of the glaze on the surface of the green body is 0.4mm; when the glaze slurry is applied to the surface of the green body, the green body is ...
Embodiment 3
[0039] 59% feldspar, 17% quartz, 17% iron ore tailings, 2% limestone, 2% kaolin and 3% ashes, the weight ratio of the components is: 2 parts K 2 O, 6 copies of AL 2 o 3 , 70 parts of SiO 2 , 3 copies of P 2 o 5 , 2 Na 2 O, 5 Fe 2 o 3 , 6 parts of CaO and 6 parts of MgO, put them into the ball mill for ball milling, add water, and the ball milling time is 9 hours. After uniform mixing and stirring and fully dissolving, the glaze slurry is obtained. The remaining 0.004% is sieved; release the above ball-milled glaze slurry from the ball mill, store it in the slurry storage tank and stir; pass the glaze slurry through a 200-mesh sieve, and apply the fully suspended glaze slurry on the surface of the body with a concentration of 42 degrees Baume , the thickness of the glaze on the surface of the green body is 0.6mm; when the glaze slurry is applied to the surface of the green body, the green body is wiped with water and dried, and the water content of the green body is cont...
PUM
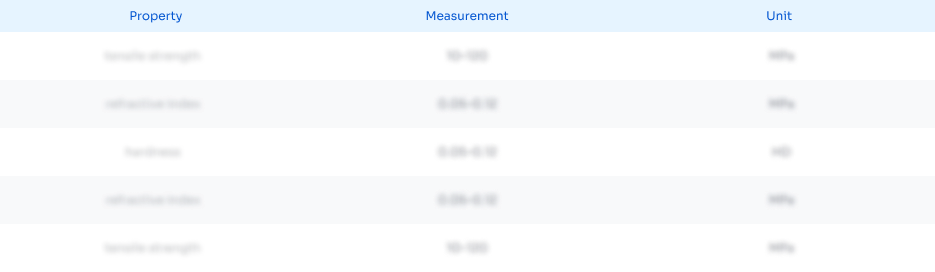
Abstract
Description
Claims
Application Information

- R&D
- Intellectual Property
- Life Sciences
- Materials
- Tech Scout
- Unparalleled Data Quality
- Higher Quality Content
- 60% Fewer Hallucinations
Browse by: Latest US Patents, China's latest patents, Technical Efficacy Thesaurus, Application Domain, Technology Topic, Popular Technical Reports.
© 2025 PatSnap. All rights reserved.Legal|Privacy policy|Modern Slavery Act Transparency Statement|Sitemap|About US| Contact US: help@patsnap.com